Technology
5 Reasons Why XCV Panel is Revolutionizing the Industry
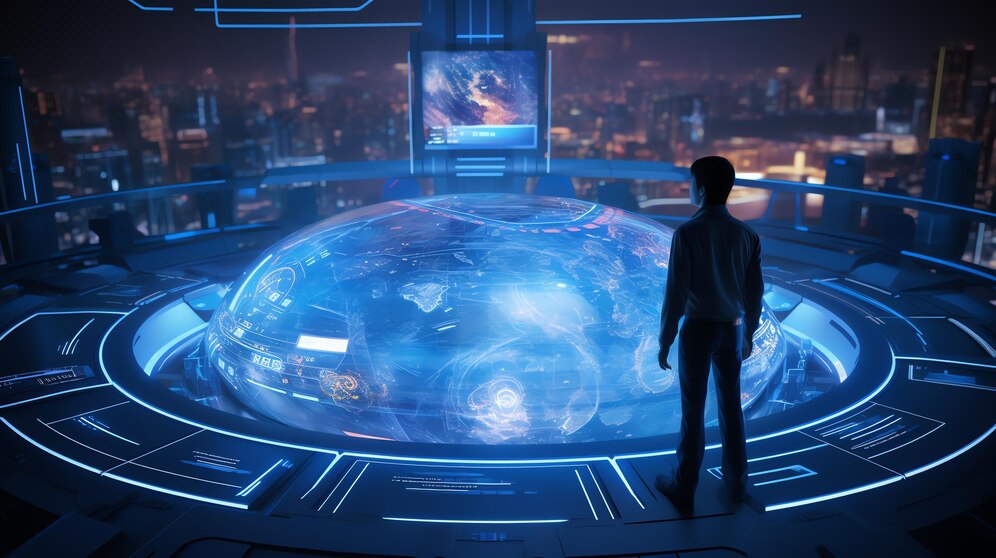
Step into the future of solar innovation with XCV Panel, where groundbreaking technology is reshaping the industry as we know it. Welcome to a new era in renewable energy that promises efficiency, sustainability, and endless possibilities.
Welcome to the Next Gen Solar Innovation: XCV Panel
Have you heard about the latest breakthrough in solar technology? The XCV Panel is here to revolutionize how we harness solar energy. With its cutting-edge design and advanced features, it’s setting a new standard in the industry.
Imagine a solar panel that not only generates electricity efficiently but also adapts to different environments seamlessly. That’s what makes the XCV Panel truly remarkable – its innovative technology allows for maximum energy production regardless of conditions.
Whether you’re looking to power your home or business with renewable energy, the XCV Panel offers unmatched performance and reliability. Say goodbye to traditional solar panels that come with limitations – embrace a smarter solution for sustainable energy generation.
Join us on this journey towards a greener future with the XCV Panel leading the way.
Innovative Technology
Welcome to the Next Gen Solar Innovation: XCV Panel
Innovative Technology is at the core of the XCV Panel, revolutionizing the solar industry with cutting-edge advancements. This next-level technology sets a new standard for efficiency and sustainability in harnessing solar power.
Understanding the XCV Panel means diving into a world of advanced solar technology that maximizes energy production while minimizing environmental impact. The intricate design and engineering behind each panel showcase unparalleled innovation within the renewable energy sector.
XCV Panel Features are redefining industry standards by integrating state-of-the-art materials and intelligent systems to optimize performance. Enhanced durability, increased output capacity, and seamless integration make these panels stand out from traditional counterparts.
How XCV Panels Work unveils their unmatched efficiency through innovative mechanisms that capture and convert sunlight into electricity with precision. The seamless operation ensures consistent energy generation even in challenging conditions, making them ideal for various applications across sectors.
Stay tuned as we delve deeper into how XCV Panels are transforming solar energy utilization across different industries and sectors!
Understanding the XCV Panel: Advanced Solar Technology
Welcome to the cutting-edge world of solar technology with the XCV Panel. This revolutionary advancement in solar energy is redefining industry standards through its advanced features and unmatched efficiency.
The XCV Panel incorporates innovative technology that sets it apart from traditional solar panels, making it a game-changer in the renewable energy sector. Its design and functionality optimize sunlight absorption, converting it into usable energy more efficiently than ever before.
By understanding how the XCV Panel leverages state-of-the-art materials and engineering techniques, we can appreciate its ability to harness solar power effectively while minimizing environmental impact. This next-generation solar solution not only benefits users financially but also contributes to a sustainable future for generations to come.
With its advanced capabilities and forward-thinking approach, the XCV Panel represents a significant step towards a cleaner, greener tomorrow powered by renewable energy sources.
XCV Panel Features Redefining Industry Standards
The XCV Panel features are truly setting a new benchmark in the solar industry. With its cutting-edge technology, these panels are redefining industry standards like never before. One standout feature is their ultra-thin design, making them lightweight and easy to install on various surfaces.
Moreover, the durability of XCV Panels is unmatched, designed to withstand harsh weather conditions and last for years without losing efficiency. The advanced materials used ensure optimal performance even in low light environments, maximizing energy production throughout the day.
Another key feature that sets XCV Panels apart is their flexibility. These panels can be seamlessly integrated into different structures and shapes, allowing for innovative solar solutions in unique spaces.
Additionally, the efficiency of XCV Panels is outstanding, generating more power per square inch compared to traditional solar panels. This increased efficiency translates to higher energy savings and quicker returns on investment for users.
In essence, the features of XCV Panels are revolutionizing how we perceive solar technology by pushing boundaries and exceeding expectations in every aspect.
How XCV Panels Work: Unleashing Unmatched Efficiency
Imagine a technology that harnesses the power of sunlight like never before – that’s exactly what XCV Panels do. These cutting-edge solar panels utilize advanced materials and design to maximize energy absorption, making them incredibly efficient.
The secret lies in their innovative construction, which allows for optimal light capture throughout the day. By converting sunlight into electricity with unmatched precision, XCV Panels can generate more power than traditional solar panels in the same amount of space.
Through a combination of high-quality components and intelligent engineering, these panels work tirelessly to produce clean and sustainable energy for a wide range of applications. Whether it’s powering homes, businesses, or even vehicles, XCV Panels are leading the way towards a greener future.
With their unparalleled efficiency and reliability, XCV Panels are revolutionizing the renewable energy industry by providing an eco-friendly solution that is both effective and accessible to all.
Transforming Solar Energy in Every Sector: XCV Panel Applications
Transforming Solar Energy in Every Sector: XCV Panel Applications
The versatility of XCV panels extends far beyond traditional solar applications. From residential rooftops to commercial buildings, these innovative panels are revolutionizing the way we harness solar energy.
In the agricultural sector, XCV panels are being used to power irrigation systems and provide sustainable energy solutions for farms. This not only reduces operational costs but also minimizes carbon footprint.
XCV panels have found their way into the transportation industry as well, with some vehicles integrating them into their design to generate power on-the-go. Imagine cars running on clean and renewable energy sourced directly from sunlight.
Even in advertising, XCV panels are making a mark by powering digital billboards and signage, offering a more eco-friendly alternative that catches attention while promoting sustainability.
When it comes to transforming solar energy across various sectors, the possibilities with XCV panels are truly endless.
From Home to Industries: XCV Panels Enhancing Various Fields
Welcome to the realm where XCV panels are transforming various fields, from homes to industries. In residential settings, XCV panels provide a sustainable energy solution that not only reduces electricity bills but also minimizes environmental impact. Homeowners can harness solar power efficiently with these advanced panels, contributing to a greener future.
Moving on to commercial and industrial sectors, XCV panels offer substantial benefits by powering operations sustainably. From manufacturing plants to office buildings, businesses can rely on this innovative technology for reliable and cost-effective energy generation. The scalability of XCV panels makes them ideal for large-scale industrial applications where high energy consumption is a constant need.
Moreover, the versatility of XCV panels extends beyond traditional settings. Industries such as agriculture and transportation are incorporating these panels into their operations to reduce costs and improve sustainability practices. With endless possibilities, XCV panels continue to revolutionize diverse fields with their efficient energy solutions.
Vehicles to Advertisement: Unique Use-Cases of XCV Panels
Have you ever imagined vehicles powered by solar energy? Well, with XCV Panels, this futuristic concept is now a reality. Imagine cars cruising down the road and charging themselves using sunlight – it’s not just eco-friendly but also cost-effective.
But it doesn’t stop there. XCV Panels are being integrated into advertising billboards to create eye-catching displays that are entirely self-sustaining. Picture a digital billboard that runs on clean energy without the need for traditional electricity sources. This innovative approach not only reduces carbon footprint but also showcases brands in a more sustainable light.
The versatility of XCV Panels extends to public transportation as well. Buses fitted with these panels can harness solar power to run internal systems, reducing reliance on fossil fuels and contributing to cleaner air quality in our cities.
From moving vehicles to stationary advertisements, the applications of XCV Panels in various industries are truly remarkable.
Practical Solutions
Installation Made Easy: A Step-by-Step Guide to Setting Up XCV Panels
Setting up XCV panels is a breeze with their user-friendly design and straightforward installation process. To begin, ensure you have the necessary tools on hand before starting the setup. The step-by-step guide provided by XCV Panel simplifies the entire installation process, making it accessible for both professionals and DIY enthusiasts.
Start by identifying the optimal location for your XCV panels – a spot that receives maximum sunlight exposure throughout the day. Securely mount the panels following the guidelines provided in the manual, ensuring they are positioned at an angle to capture sunlight efficiently.
Connect the panels correctly to your existing solar system or power grid, double-checking all connections for accuracy. Once everything is in place, power up your XCV panels and witness firsthand how they start converting sunlight into clean energy immediately.
With their easy installation process and clear instructions, incorporating XCV panels into your energy system has never been simpler. Experience the convenience of sustainable energy production with XCV Panel’s practical solutions today!
Installation Made Easy: A Step-by-Step Guide to Setting Up XCV Panels
Setting up XCV panels is a straightforward process that anyone can do with the right guidance. To begin, choose a location with optimal sunlight exposure for maximum efficiency. Ensure the area is clear of any obstructions like trees or buildings.
Next, carefully unpack the XCV panels and lay them out according to the installation diagram provided. Connect the panels together using the designated cables and connectors. Double-check all connections to avoid any issues later on.
Mounting the panels securely is crucial for their performance. Follow the instructions to attach them firmly to either a roof or ground-based mounting system. Make sure they are angled correctly towards the sun for optimal energy absorption.
Once everything is in place, connect your XCV panels to an inverter and then to your electrical system. Test the setup to ensure it’s functioning properly before enjoying clean and renewable energy from your new XCV panels!
Future Potential
As we look towards the future of solar energy, the XCV Panel stands out as a game-changer in the industry. Its innovative technology and unmatched efficiency are paving the way for new possibilities in renewable energy solutions.
With its advanced features and practical applications across various sectors, the XCV Panel is poised to revolutionize how we harness solar power for years to come. From residential homes to large-scale industrial projects, this cutting-edge technology offers a sustainable and cost-effective alternative to traditional energy sources.
As we continue to explore new ways to reduce our carbon footprint and combat climate change, the XCV Panel presents an exciting opportunity to make significant strides towards a greener future. By leveraging its unique capabilities and versatility, we can unlock endless potential for clean energy generation on a global scale.
The future holds immense promise for the XCV Panel as it continues to push boundaries and redefine what’s possible in renewable energy innovation. Stay tuned as we witness this revolutionary technology shape the landscape of sustainability in remarkable ways.
Conclusion
XCV Panel is undoubtedly revolutionizing the solar industry with its innovative technology, advanced features, and unmatched efficiency. From transforming energy generation in various sectors to offering practical solutions for easy installation, XCV Panels are setting new standards for solar power utilization. The future potential of XCV Panels is limitless, promising a sustainable and efficient way to harness solar energy for years to come. Embrace the Next Gen Solar Innovation with XCV Panel and be part of the green energy revolution today!
Technology
The Scale Blank: How to choose Perfect One for Your Needs
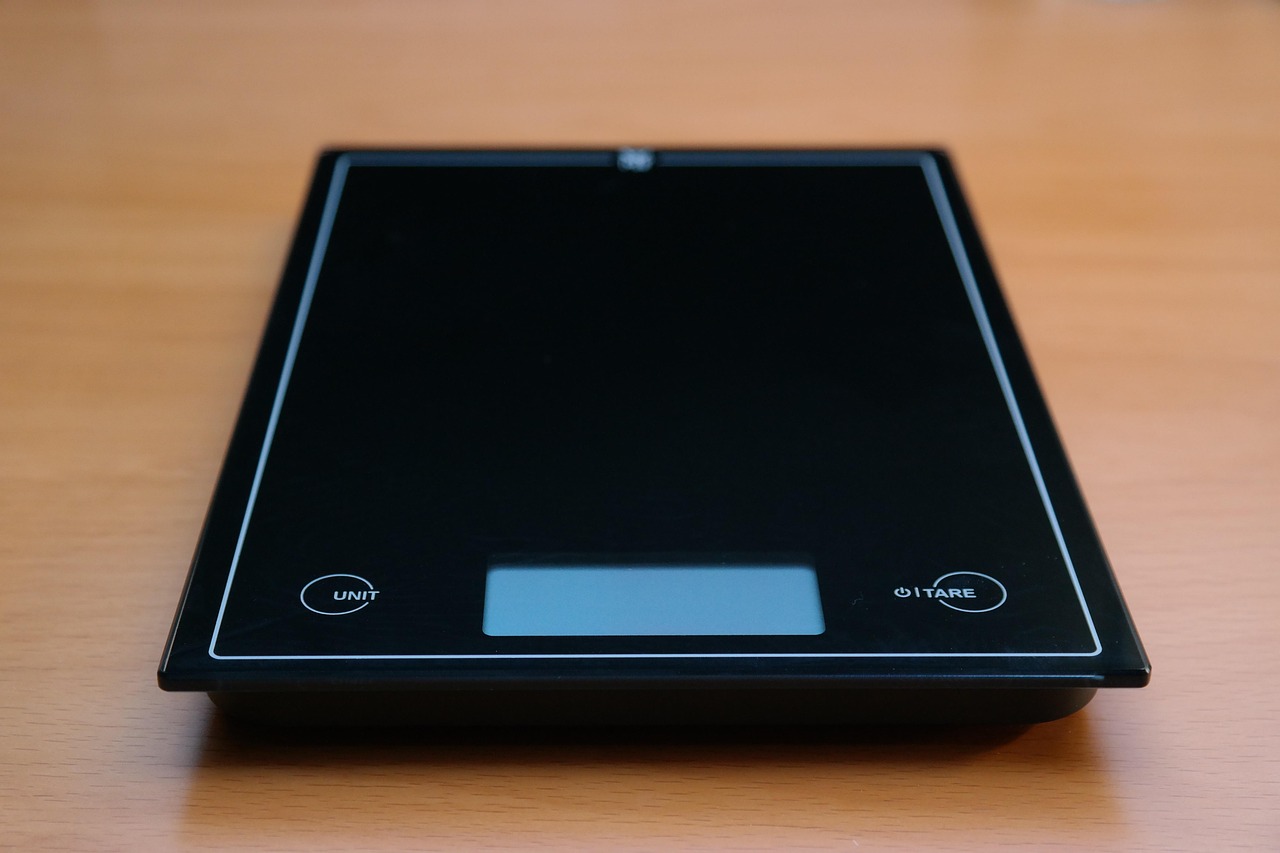
Have you ever wondered why some kitchen scales perform flawlessly while others fail within months? The secret often lies in an overlooked component—the scale blank. Whether you’re a home cook, a professional chef, or a business owner, choosing the right scale blank can make all the difference in accuracy, durability, and performance.
In this guide, we’ll break down everything you need to know about scale blanks—what they are, why they matter, and how to pick the best one for your needs.
What Is a Scale Blank?
A scale blank is the foundational platform of a weighing scale where items are placed for measurement. It’s the flat surface (usually made of stainless steel, glass, or plastic) that interacts directly with whatever you’re weighing.
Why Does It Matter?
-
Accuracy: A poorly designed blank can flex or warp, leading to incorrect readings.
-
Durability: The material determines how well it resists scratches, stains, and wear.
-
Hygiene: Some blanks are easier to clean, making them ideal for food or medical use.
Types of Scale Blanks: Pros and Cons
Not all scale blanks are created equal. Here’s a breakdown of the most common types:
1. Stainless Steel Blanks
✅ Pros:
-
Highly durable and resistant to corrosion
-
Easy to clean (ideal for kitchens and labs)
-
Provides a stable weighing surface
❌ Cons:
-
Can be slippery for lightweight items
-
Prone to fingerprints and smudges
Best for: Commercial kitchens, laboratories, and industrial settings.
2. Glass Blanks
✅ Pros:
-
Sleek, modern appearance
-
Easy to wipe clean
-
Doesn’t absorb odors or stains
❌ Cons:
-
Fragile—can crack under heavy weight
-
Slippery for certain items
Best for: Home kitchens, bakeries, and retail displays.
3. Plastic Blanks
✅ Pros:
-
Lightweight and affordable
-
Resistant to minor impacts
-
Non-slip surface in some models
❌ Cons:
-
Less durable over time
-
Can absorb stains and odors
Best for: Budget-friendly home scales or portable options.
How to Choose the Right Scale Blank
Picking the best scale blank depends on your specific needs. Here’s what to consider:
1. Intended Use
-
Cooking/Baking? Stainless steel or glass for easy cleaning.
-
Industrial Weighing? Reinforced stainless steel for durability.
-
Portable Scale? Lightweight plastic for convenience.
2. Weight Capacity
-
Small kitchen scales (1–10 lbs): Glass or plastic.
-
Heavy-duty scales (50+ lbs): Thick stainless steel.
3. Maintenance & Cleaning
-
Stainless steel: Wipe with a damp cloth.
-
Glass: Use glass cleaner for shine.
-
Plastic: Avoid abrasive cleaners to prevent scratches.
4. Anti-Slip Features
Some blanks have textured surfaces or rubberized edges to prevent items from sliding off.
5. Budget
-
Premium: Stainless steel
-
Mid-range: Tempered glass
-
Budget-friendly: High-quality plastic
Real-World Examples: Where Scale Blanks Make a Difference
Example 1: Bakery Business
A bakery switched from plastic to stainless steel blanks and saw fewer inaccuracies in dough measurements, leading to more consistent products.
Example 2: Home Cooks
A home chef using a glass scale blank found it easier to clean after measuring sticky ingredients like honey or syrup.
Example 3: Lab Environments
A research lab using high-grade stainless steel blanks avoided corrosion from chemical spills, ensuring long-term reliability.
Expert Tips for Maintaining Your Scale Blank
To extend the lifespan of your scale blank:
✔ Clean regularly—avoid buildup of debris.
✔ Avoid overloading—stick to the maximum weight limit.
✔ Store properly—keep in a dry place to prevent rust (for metal blanks).
✔ Check for damage—cracks or warping can affect accuracy.
Final Thoughts: Why Your Scale Blank Choice Matters
The scale blank might seem like a small detail, but it plays a crucial role in the accuracy and longevity of your weighing scale. Whether you’re a home cook, a business owner, or a lab technician, choosing the right material and maintaining it properly ensures reliable measurements every time.
Ready to upgrade your scale? Now that you know what to look for, you can make an informed decision and get the best performance out of your weighing device.
FAQs About Scale Blanks
Can I replace a damaged scale blank?
Yes, many manufacturers sell replacement blanks. Check compatibility before purchasing.
Are there antimicrobial scale blanks?
Some stainless steel blanks have antimicrobial coatings, ideal for medical or food industries.
How do I know if my scale blank is affecting accuracy?
If your scale gives inconsistent readings, inspect the blank for warping or damage.
Technology
Why You Need to Check Out the Socks5 Proxy List Wingate.me
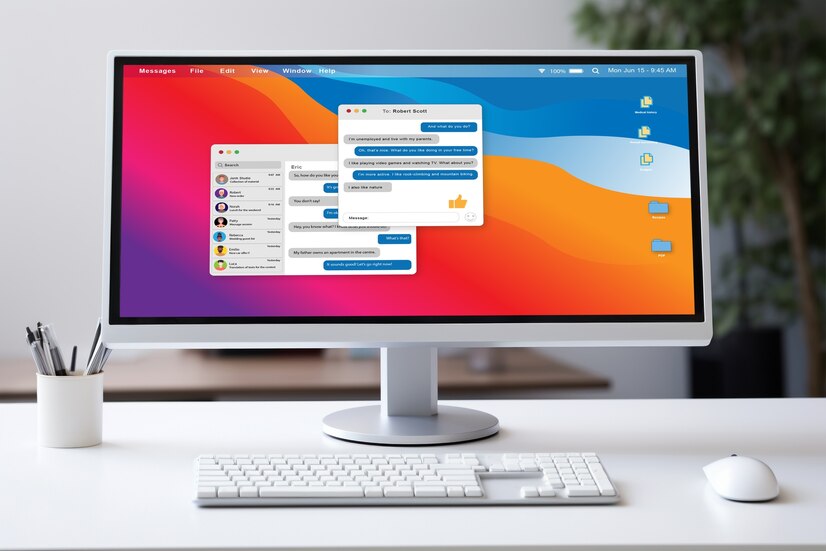
Looking to enhance your online security and privacy? Dive into the world of private proxies with Wingate.me’s Socks5 Proxy List! Whether you’re a seasoned web user or just starting out, this comprehensive list offers unparalleled protection and browsing freedom. Let’s explore why checking out Wingate.me’s Socks5 Proxy List is a game-changer for your online experience.
Navigation Menu
When it comes to navigating Wingate.me’s Socks5 Proxy List, the user-friendly interface makes finding what you need a breeze. The navigation menu is thoughtfully designed for easy access to various features and options, ensuring a seamless browsing experience. With clear labels and intuitive organization, you can quickly locate specific tools or settings without any hassle.
The menu layout allows users to navigate effortlessly between different sections of the proxy list, making it simple to switch between saved searches, repository files, latest commits, and more. Whether you’re a beginner or an advanced user, the navigation menu caters to all levels of expertise with its straightforward design and functionality.
By utilizing the navigation menu effectively, users can maximize their productivity and efficiency when exploring Wingate.me’s Socks5 Proxy List. Take advantage of this well-structured tool to streamline your browsing experience and unlock the full potential of private proxies for enhanced online security and privacy.
Use Saved Searches to Filter Your Results More Quickly
When browsing through a socks5 proxy list on Wingate.me, efficiency is key. One handy feature to streamline your search process is utilizing saved searches to filter results quickly. By saving specific search criteria such as location, speed, or anonymity level, you can access relevant proxies in just a few clicks.
This time-saving tool ensures that you don’t have to input the same filters repeatedly every time you revisit the site. Simply set your preferences once and let Wingate.me do the rest. Whether you’re looking for proxies for data scraping, geo-blocked content access, or cybersecurity purposes, using saved searches can help tailor your results to meet your exact needs.
With this functionality at your disposal, finding the perfect socks5 proxy becomes a breeze. Say goodbye to sifting through irrelevant options – optimize your search experience with saved searches on Wingate.me today!
Folders and Files
When it comes to navigating through the Socks5 Proxy List on Wingate.me, understanding the organization of folders and files is key. Each folder contains a specific category of proxies, neatly arranged for easy access. From streaming proxies to gaming proxies, you can find them all conveniently sorted within their respective folders.
Files within each folder provide detailed information about each proxy, including its speed, location, and anonymity level. This allows users to make informed decisions when selecting the right proxy for their needs. Whether you’re looking for fast speeds or reliable connections, exploring the various files in each folder can help you find the perfect match.
By utilizing the intuitive folder and file structure on Wingate.me’s Socks5 Proxy List, users can efficiently browse through different categories and options available to them. Easy navigation means less time searching and more time enjoying seamless proxy connections for all your online activities.
Latest Commit
Are you someone who always wants to stay up-to-date with the latest changes in your favorite projects? Well, at Wingate.me, we understand the importance of keeping track of the “Latest Commit” on our Socks5 Proxy List repository.
The “Latest Commit” feature allows you to see the most recent updates made to our proxy list, giving you real-time insights into any new additions or modifications. Whether it’s bug fixes, performance enhancements, or exciting new features, staying informed about the latest commit can help you make informed decisions when choosing proxies for your online activities.
By regularly checking out the latest commit section on Wingate.me’s platform, you can ensure that you are always using the most updated and optimized version of our socks5 proxy list. Stay ahead of the game and maximize your browsing experience by staying connected to our repository’s latest developments!
History
Have you ever wondered about the history of a website or online platform? The “History” section on Wingate.me provides valuable insights into past activities and changes made to the Socks5 proxy list. It’s like taking a trip down memory lane, seeing how the service has evolved over time.
By exploring this feature, users can track updates, modifications, and improvements implemented by Wingate.me. This historical perspective allows for a better understanding of how the platform has developed and adapted to meet user needs effectively.
Delving into the History section offers transparency and accountability as users can trace back any alterations or additions that have been made. It adds a layer of trust and reliability to the overall service provided by Wingate.me.
Repository Files Navigation
When it comes to navigating through repository files on Wingate.me, efficiency is key. The platform offers a seamless experience for users to locate and access specific files within their repositories effortlessly.
With intuitive search functionalities and organized file structures, finding the exact document you need becomes a breeze. Whether you’re looking for code snippets, configuration files, or any other data stored in your repository, Wingate.me streamlines the process.
By providing clear pathways to navigate through folders and subfolders, users can quickly drill down to the desired file without wasting time on unnecessary clicks. This user-friendly approach enhances productivity and ensures that developers can focus on their tasks rather than getting lost in complex directory structures.
Wingate.me’s repository files navigation feature simplifies file management and facilitates smooth collaboration among team members working on shared projects.
Releases
When it comes to the “Releases” section on Wingate.me’s Socks5 Proxy List, users can stay updated on the latest changes and improvements. This feature allows for easy tracking of when new versions or updates are launched, ensuring that you have access to the most current resources available.
By regularly checking the “Releases” tab, you can see any bug fixes, enhancements, or additional features that have been implemented into the proxy list. This transparency enables users to understand what modifications have been made and how they may impact their browsing experience.
Whether it’s a minor tweak or a significant upgrade, staying informed through the “Releases” section ensures that you are always aware of any advancements in Wingate.me’s Socks5 Proxy List. Stay ahead by keeping an eye on this section for any new developments that could benefit your proxy usage.
Packages
When it comes to exploring the functionalities and utilities of Wingate.me, the “Packages” feature stands out as a valuable tool for users. This section provides access to various pre-packaged sets of resources, tools, or configurations that can streamline your workflow and enhance your browsing experience.
By accessing packages through Wingate.me, users can easily integrate additional features or enhancements into their proxy setup without the hassle of manual configuration. Whether you’re looking for security add-ons, performance optimizations, or specialized tools, the Packages section offers a curated selection to choose from.
Each package is designed to cater to specific needs and preferences, allowing users to customize their proxy settings according to their requirements. From enhancing privacy protocols to optimizing connection speeds, these packages offer a convenient way to enhance your online activities effortlessly.
Exploring the Packages section on Wingate.me opens up a world of possibilities for maximizing the efficiency and effectiveness of your proxy usage. Unlock new capabilities and functionalities with just a few clicks in this dynamic repository of resources tailored for discerning users like yourself.
Footer
The footer section on a website might seem small, but it plays a significant role in user experience. It’s the final impression visitors have before leaving your site. The footer is like the cherry on top of a sundae – a finishing touch that ties everything together.
In the footer, you can find important links like contact information, privacy policies, terms and conditions, and social media icons for easy navigation. These elements help users feel more comfortable exploring your site and potentially converting into customers.
Design-wise, the footer can also showcase your brand’s personality through color schemes, fonts, and creative layouts. A well-designed footer not only looks professional but also enhances the overall aesthetics of your website.
Don’t underestimate the power of a well-crafted footer – it may be at the bottom of the page, but its impact on user engagement and satisfaction is anything but minor.
What Is A Socks5 Proxy?
Have you ever wondered how to enhance your online privacy and security while browsing the internet? Well, a Socks5 proxy might just be the solution you’re looking for.
In simple terms, a Socks5 proxy acts as an intermediary server between your device and the internet. When you connect to the internet through a Socks5 proxy, your IP address is masked, making it harder for websites to track your online activities.
Unlike traditional proxies, Socks5 proxies are highly versatile and can handle various types of traffic such as HTTP, HTTPS, FTP, and more. This flexibility makes them ideal for tasks like torrenting or accessing geo-restricted content.
Additionally, Socks5 proxies offer faster speeds and better performance compared to other proxy options. With its advanced features and benefits, using a Socks5 proxy can significantly improve your online experience by providing an extra layer of anonymity and security.
What Is Private Proxy Wingate.me?
Private Proxy Wingate.me offers a secure way to browse the internet anonymously. With this service, users can mask their IP addresses, enhancing privacy and security online. By utilizing private proxies, individuals can access websites without revealing their true location or identity.
Wingate.me’s private proxy service allows for seamless browsing without restrictions. Whether you’re accessing geo-blocked content or simply prioritizing your privacy, these proxies provide a reliable solution. Through encrypted connections, Wingate.me ensures that your data remains protected while surfing the web.
With Private Proxy Wingate.me, users can enjoy faster connection speeds and reduced latency compared to public proxies. This advantage is especially beneficial for activities like streaming or online gaming where performance matters. Additionally, Wingate.me offers dedicated customer support to assist with any technical issues that may arise when using their private proxy services.
In today’s digital landscape where privacy is paramount, Private Proxy Wingate.me stands out as a trusted provider of secure internet browsing solutions.
Types of Private Proxy Wingate.me
When it comes to private proxies, Wingate.me offers a variety of options to suit different needs and preferences.
One type of private proxy available on Wingate.me is the dedicated proxy. This type allocates a single IP address exclusively for your use, providing enhanced security and reliability for your online activities.
Another option is the rotating proxy offered by Wingate.me. With this type, you can automatically switch between multiple IP addresses at set intervals, allowing you to access diverse geo-locations and avoid detection.
Moreover, Wingate.me also provides shared proxies which are cost-effective solutions for those looking to mask their online identity without breaking the bank.
Each type of private proxy from Wingate.me caters to specific requirements, whether it’s individualized security measures or budget-friendly anonymity.
An Overview Of Wingate.me’s Socks5 Proxy List
At Wingate.me, the Socks5 proxy list is a powerful tool for enhancing your online security and privacy. This list provides users with access to a vast array of high-speed proxies that can help mask their IP addresses and encrypt their internet traffic. With the Socks5 protocol, you can enjoy fast and reliable connections while keeping your browsing activities anonymous.
The Socks5 proxy list offered by Wingate.me is regularly updated to ensure that users have access to the latest and most secure proxies available. Whether you’re looking to bypass geo-restrictions, protect your personal information from prying eyes, or simply enhance your online anonymity, this proxy list has got you covered.
By utilizing Wingate.me’s Socks5 proxy list, you can take control of your online experience and browse the web with confidence. Stay safe and secure while enjoying unrestricted access to content from around the globe.
The Benefits of Wingate.me’s Socks5 Proxy List
When it comes to online security and anonymity, Wingate.me’s Socks5 Proxy List offers a range of benefits that users can take advantage of. One key benefit is the enhanced level of privacy it provides by masking your IP address, making it harder for third parties to track your online activities.
Another advantage is the ability to bypass geo-restrictions and access content that may be blocked in your region. This can be particularly useful for streaming services or websites with regional restrictions.
Moreover, Wingate.me’s Socks5 Proxy List offers faster connection speeds compared to other proxy types, ensuring smooth browsing and minimal lag while maintaining a secure connection. This can be crucial for tasks that require high bandwidth or real-time data transfer.
Additionally, using Wingate.me’s Socks5 Proxy List adds an extra layer of security when connecting to public Wi-Fi networks, protecting your sensitive information from potential threats such as hackers or malicious software.
How To Set Up Wingate.me’s Socks5 Proxy?
Setting up Wingate.me’s Socks5 proxy is a straightforward process that allows you to enhance your online privacy and security. To begin, you first need to visit the Wingate.me website and sign up for an account. Once registered, navigate to the dashboard where you can access the list of available proxies.
Next, select the Socks5 proxy option from the menu and choose a server location that best suits your needs. After selecting a server, you will be provided with detailed instructions on how to configure your device or browser settings to connect to the chosen proxy.
Follow these instructions carefully, inputting the required information such as IP address, port number, username, and password. Once set up correctly, your internet traffic will be routed through Wingate.me’s secure Socks5 proxy server seamlessly.
By utilizing Wingate.me’s Socks5 proxy, you can enjoy enhanced anonymity and protection while browsing online.
Conclusion
In a world where online privacy and security are paramount, having access to a reliable socks5 proxy list like Wingate.me is essential. By utilizing Wingate.me’s private proxy services, you can enhance your online anonymity and protect your sensitive information from prying eyes.
With various types of private proxies available, including socks5 proxies, Wingate.me offers flexibility and customization to suit your specific needs. Whether you’re looking to bypass geo-restrictions, improve your browsing speed, or simply add an extra layer of security to your online activities, Wingate.me has got you covered.
Setting up Wingate.me’s socks5 proxy is quick and easy, allowing you to start benefiting from enhanced privacy and security in no time. Simply follow the straightforward instructions provided by Wingate.me to configure the socks5 proxy on your preferred device or browser.
Don’t compromise on your online safety – explore Wingate.me’s socks5 proxy list today and take control of your digital footprint. Stay protected, stay secure with Wingate.me!
Technology
Maple Juicer: Ultimate Guide to Tapping Nature’s Sweetest Nectar
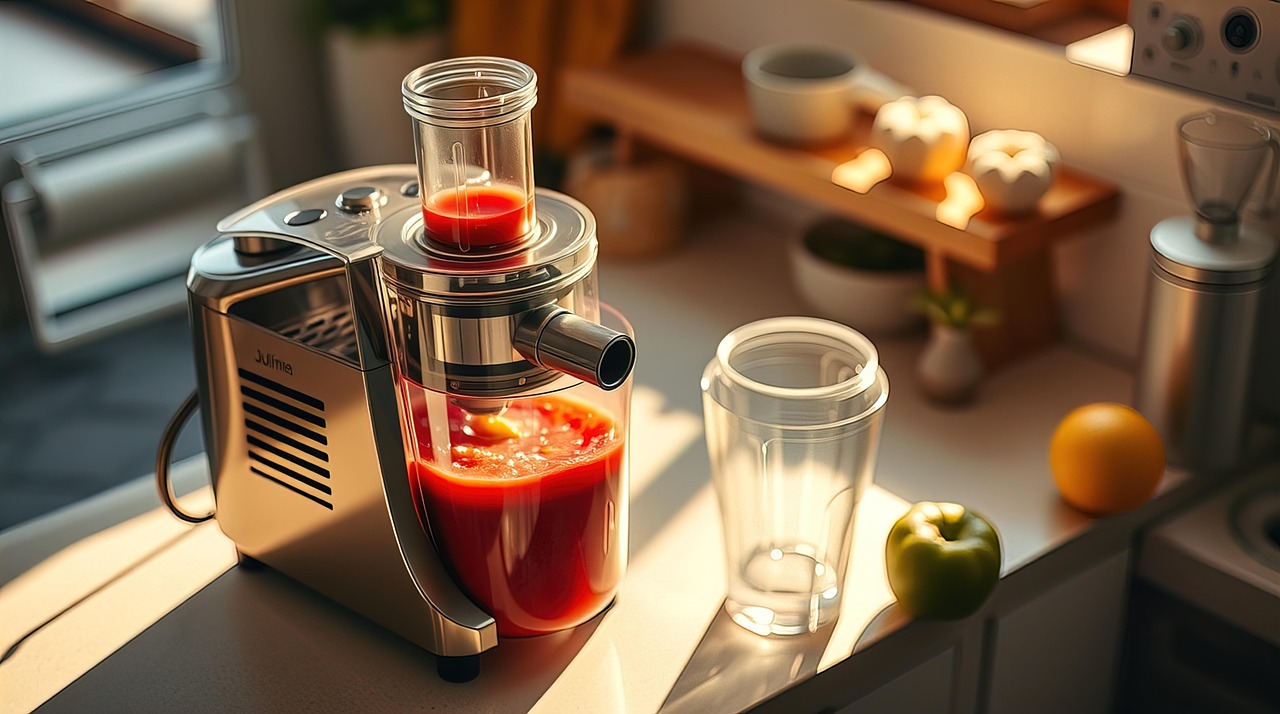
Have you ever wondered how that rich, golden maple syrup drizzled over your pancakes makes its way from tree to table? The secret lies in a simple yet ingenious tool—the maple juicer. Whether you’re a hobbyist, a homesteader, or a small-scale syrup producer, mastering the art of maple juicing can be incredibly rewarding.
In this guide, we’ll walk you through everything you need to know about maple juicers—from how they work to expert tips for maximizing your syrup yield. Let’s dive in!
What Is a Maple Juicer?
A maple juicer (or maple tap) is a device used to extract sap from sugar maple trees, which is then boiled down into delicious maple syrup. While the concept is centuries old, modern tools have made the process more efficient and accessible.
How Does It Work?
-
Tapping the Tree – A small hole is drilled into the maple tree.
-
Inserting the Spile – A spout (or “spile”) is placed into the hole to direct sap into a collection container.
-
Collecting the Sap – Sap flows out during warm days and cold nights (typically late winter to early spring).
-
Boiling Down – The collected sap is boiled to evaporate water, leaving pure maple syrup.
Types of Maple Juicers & Tapping Systems
Not all maple juicers are created equal. Here’s a breakdown of the most common types:
1. Traditional Bucket & Spile System
-
Best for: Small-scale hobbyists
-
How it works: Metal or plastic spiles drip sap into hanging buckets.
-
Pros: Low-cost, simple setup
-
Cons: Manual collection, risk of contamination
2. Tubing Systems with Vacuum Pumps
-
Best for: Medium to large-scale producers
-
How it works: A network of tubes connects multiple trees to a central collection tank, sometimes with a vacuum pump to increase yield.
-
Pros: Higher sap yield, less labor-intensive
-
Cons: More expensive, requires maintenance
3. Plastic Bag Systems
-
Best for: Beginners testing the waters
-
How it works: Disposable bags attach to spiles for easy sap collection.
-
Pros: Lightweight, no cleaning needed
-
Cons: Less durable, not ideal for high yields
How to Choose the Best Maple Juicer for Your Needs
Picking the right system depends on your goals, budget, and scale. Consider these factors:
✅ Budget – Bucket systems are cheapest, while tubing setups require investment.
✅ Number of Trees – Small operations (1-10 trees) can use buckets; larger setups benefit from tubing.
✅ Labor vs. Automation – Vacuum systems save time but need upkeep.
✅ Local Climate – Colder regions may need insulated tubing to prevent freezing.
Expert Tips for Maximizing Your Maple Sap Yield
Want to get the most out of your maple juicer? Follow these proven strategies:
1. Tap at the Right Time
-
Sap flows best when daytime temps are above freezing (40°F/4°C) and nights drop below freezing (20°F/-6°C).
-
In most regions, late February to early April is prime tapping season.
2. Choose Healthy, Mature Trees
-
Ideal trees are at least 10-12 inches in diameter (one tap per tree).
-
Larger trees (18+ inches) can handle two taps.
3. Drill the Perfect Hole
-
Use a sharp, clean drill bit (7/16″ or 5/16″ for smaller taps).
-
Drill at a slight upward angle (5-10°) to help sap flow.
4. Keep It Clean
-
Sanitize taps and buckets to prevent bacterial growth (a mix of 1-part bleach to 20-parts water works well).
-
Replace tubing every few years to avoid mold buildup.
5. Use a Vacuum System (If Possible)
-
Studies show vacuum-assisted tapping can increase sap yield by 50-100%!
Common Mistakes to Avoid
🚫 Tapping Too Early or Late – Miss the sap run, and you’ll get little to no yield.
🚫 Over-Tapping Small Trees – Damages the tree and reduces future sap production.
🚫 Poor Storage – Sap spoils quickly; refrigerate or boil within 24-48 hours.
🚫 Ignoring Weather Changes – A sudden warm spell can end the season early.
Real-World Success Story: From Backyard Hobby to Small Business
Meet Jake & Emily, a Vermont couple who started with five maple trees and a bucket system. After a few years of experimenting, they upgraded to a 300-tree tubing setup with a vacuum pump.
Their results?
-
Year 1: 5 trees → 1 gallon of syrup
-
Year 5: 300 trees → 75+ gallons of syrup (sold at local farmers’ markets)
Their secret? Starting small, learning from mistakes, and scaling wisely.
Final Thoughts: Is Maple Juicing Right for You?
Whether you’re a DIY enthusiast, a homesteader, or an aspiring syrup producer, tapping maple trees is a fulfilling (and delicious!) endeavor. With the right tools, timing, and techniques, you can turn your backyard into a mini syrup operation.
Ready to start? Grab a maple juicer, pick a healthy tree, and let nature’s sweetness flow!
-
Articles3 months ago
How Many Times Can You Regrow Green Onions
-
News10 months ago
Understanding HotLeaks: What You Need to Know
-
Fashion8 months ago
Opals in the USA: A Gemstone Transforming the Crystal Healing Market
-
Entertainment7 months ago
How to Use Snaptik: A Complete Guide to Download TikTok Videos
-
Technology1 year ago
The Wonders of Oh Em Gee Blog
-
Entertainment1 year ago
Bare it All: Unforgettable Skinny Dipping Stories Shared
-
Health1 year ago
Can You Smoke Shrooms? Exploring the Myths and Realities
-
Articles5 months ago
WHAT IS THE DIFFERENCE BETWEEN SEED GARLIC AND FOOD GARLIC?