Technology
4 Considerations You Must Know Before Investing in Bending Machines
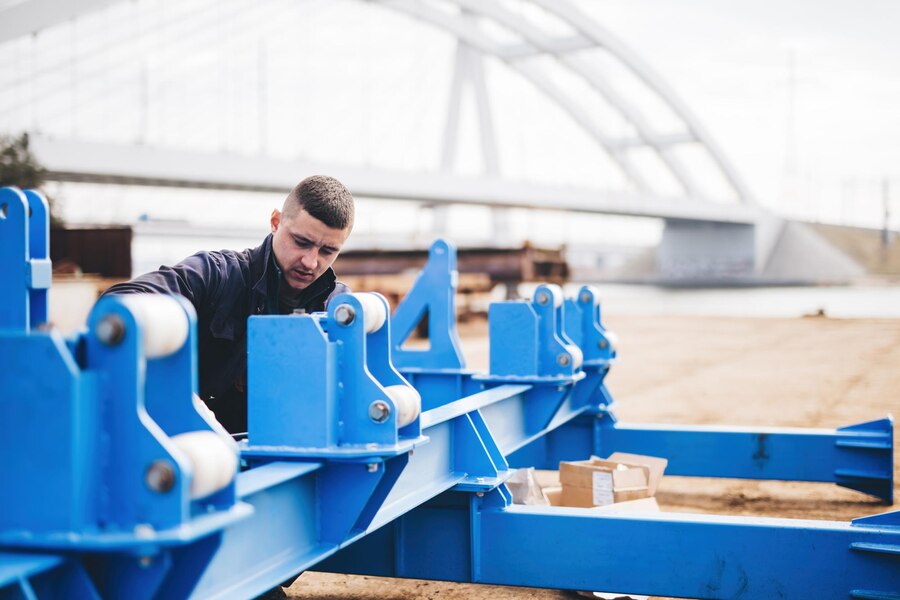
Are you considering adding bending machines to your operations? These powerful tools play a critical role in shaping metal and other materials with precision. However, before making an investment, there are key factors that require careful attention.
Taking the time to understand these considerations can help you make informed decisions. A thoughtful approach ensures the best fit for your needs and goals. In this blog, we will tackle 4 considerations you must know before investing in bending machines.
1. Understanding the Material Capabilities and Limitations of Bending Machines
Bending machines are made of specific materials, so picking the right one is important. Knowing the thickness of the material helps you choose the best machine. Not all machines can bend every material, so they must match the job.
Materials have different strengths, which affects how easy they are to bend. Some, like soft metals, bend easily, while others, like steel, are harder to work with. This difference helps you find the machine that works best for your material.
It is important to know what your machine can handle. Each bending machine has a limit on how thick or strong a material it can bend. Knowing this helps you plan your work and avoid damage to the machine.
2. Assessing the Production Volume and Required Efficiency for Your Operations
When investing in a bending machine, think about mass production needs. Will you use it often or just occasionally? Higher machine capacity might be better for busy operations.
Efficient production is crucial for success. You need machines that can keep up. Evaluate how many bends you need to make daily.
Evaluate how quickly the machine can bend. This impacts your overall workflow. A smooth process helps in meeting your production goals.
3. Evaluating the Costs: Upfront Investment and Long-Term Maintenance
Investing in bending machines is a significant investment. It is not only about buying the machine. Consider maintenance costs as well.
Check upfront costs versus long-term savings. Affordable machines may cost more over time. Higher-quality pipe benders might save money later.
Always budget for repairs and parts replacement. Machines need regular care. Ensuring ease of use ensures they work longer and better.
4. Analyzing the Technological Features and Automation Potential of Modern Models
The latest bending machines have great features that make work easier. Many models include automation, which speeds up production time. This helps businesses meet deadlines while keeping quality high.
When choosing a bending machine, look for one that is easy to use. Machines that are simple to operate help reduce mistakes during production. This saves time and lets workers do their jobs more efficiently.
Automation is a big benefit when picking a bending machine. It reduces the need for manual work, making things faster and smoother. This leads to more work done and lower costs for the business.
Make Smart Choices with Bending Machines
Bending machines are essential tools that can enhance your operations when chosen wisely. Before purchasing, think about the materials you’ll work with and the production volume you need. Matching the machine’s features to your specific requirements ensures it will perform effectively.
Consider both the initial cost and long-term maintenance of the machine. Investing in a reliable, high-quality model can save you money over time. Prioritizing ease of use and automation features will improve efficiency and help meet your production goals.
Did you find this article helpful? Visit more of our blogs!
Technology
The Scale Blank: How to choose Perfect One for Your Needs
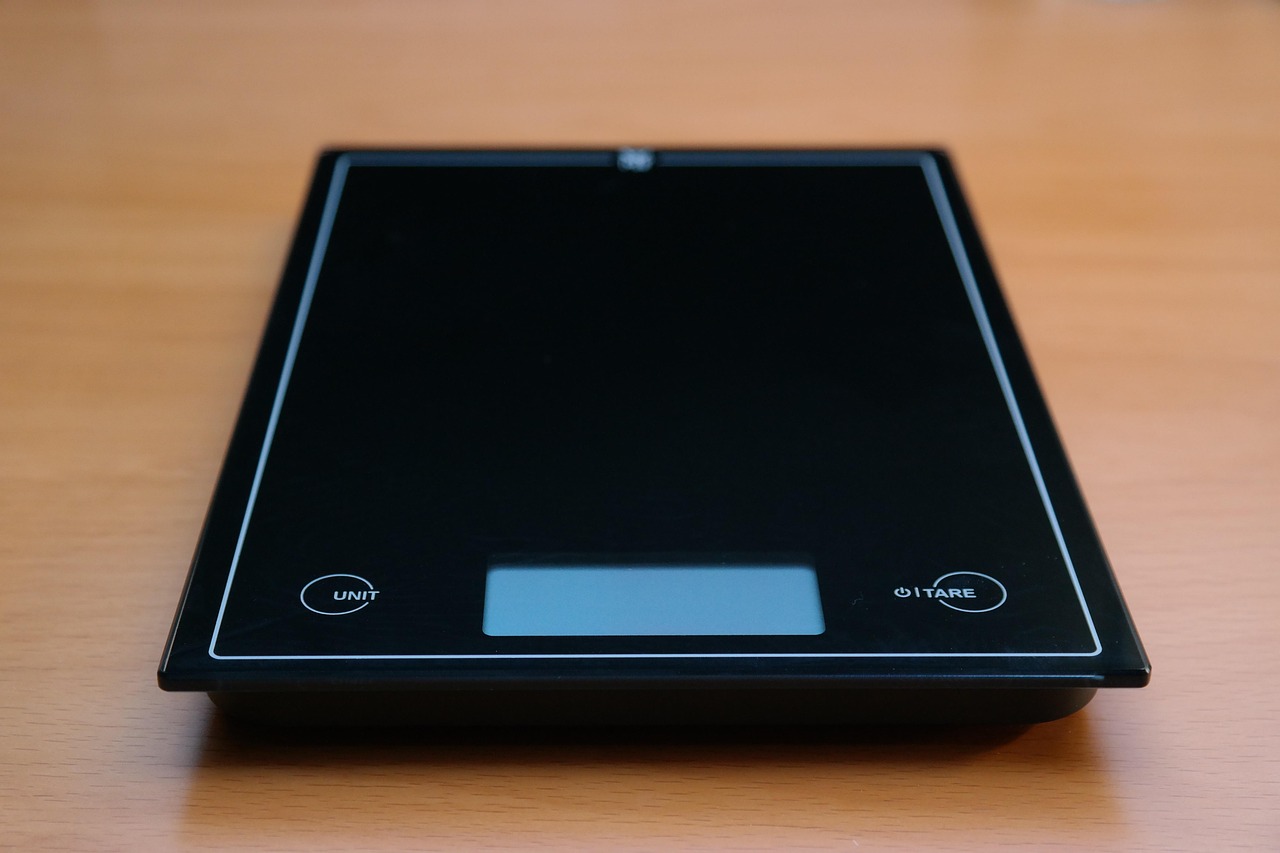
Have you ever wondered why some kitchen scales perform flawlessly while others fail within months? The secret often lies in an overlooked component—the scale blank. Whether you’re a home cook, a professional chef, or a business owner, choosing the right scale blank can make all the difference in accuracy, durability, and performance.
In this guide, we’ll break down everything you need to know about scale blanks—what they are, why they matter, and how to pick the best one for your needs.
What Is a Scale Blank?
A scale blank is the foundational platform of a weighing scale where items are placed for measurement. It’s the flat surface (usually made of stainless steel, glass, or plastic) that interacts directly with whatever you’re weighing.
Why Does It Matter?
-
Accuracy: A poorly designed blank can flex or warp, leading to incorrect readings.
-
Durability: The material determines how well it resists scratches, stains, and wear.
-
Hygiene: Some blanks are easier to clean, making them ideal for food or medical use.
Types of Scale Blanks: Pros and Cons
Not all scale blanks are created equal. Here’s a breakdown of the most common types:
1. Stainless Steel Blanks
✅ Pros:
-
Highly durable and resistant to corrosion
-
Easy to clean (ideal for kitchens and labs)
-
Provides a stable weighing surface
❌ Cons:
-
Can be slippery for lightweight items
-
Prone to fingerprints and smudges
Best for: Commercial kitchens, laboratories, and industrial settings.
2. Glass Blanks
✅ Pros:
-
Sleek, modern appearance
-
Easy to wipe clean
-
Doesn’t absorb odors or stains
❌ Cons:
-
Fragile—can crack under heavy weight
-
Slippery for certain items
Best for: Home kitchens, bakeries, and retail displays.
3. Plastic Blanks
✅ Pros:
-
Lightweight and affordable
-
Resistant to minor impacts
-
Non-slip surface in some models
❌ Cons:
-
Less durable over time
-
Can absorb stains and odors
Best for: Budget-friendly home scales or portable options.
How to Choose the Right Scale Blank
Picking the best scale blank depends on your specific needs. Here’s what to consider:
1. Intended Use
-
Cooking/Baking? Stainless steel or glass for easy cleaning.
-
Industrial Weighing? Reinforced stainless steel for durability.
-
Portable Scale? Lightweight plastic for convenience.
2. Weight Capacity
-
Small kitchen scales (1–10 lbs): Glass or plastic.
-
Heavy-duty scales (50+ lbs): Thick stainless steel.
3. Maintenance & Cleaning
-
Stainless steel: Wipe with a damp cloth.
-
Glass: Use glass cleaner for shine.
-
Plastic: Avoid abrasive cleaners to prevent scratches.
4. Anti-Slip Features
Some blanks have textured surfaces or rubberized edges to prevent items from sliding off.
5. Budget
-
Premium: Stainless steel
-
Mid-range: Tempered glass
-
Budget-friendly: High-quality plastic
Real-World Examples: Where Scale Blanks Make a Difference
Example 1: Bakery Business
A bakery switched from plastic to stainless steel blanks and saw fewer inaccuracies in dough measurements, leading to more consistent products.
Example 2: Home Cooks
A home chef using a glass scale blank found it easier to clean after measuring sticky ingredients like honey or syrup.
Example 3: Lab Environments
A research lab using high-grade stainless steel blanks avoided corrosion from chemical spills, ensuring long-term reliability.
Expert Tips for Maintaining Your Scale Blank
To extend the lifespan of your scale blank:
✔ Clean regularly—avoid buildup of debris.
✔ Avoid overloading—stick to the maximum weight limit.
✔ Store properly—keep in a dry place to prevent rust (for metal blanks).
✔ Check for damage—cracks or warping can affect accuracy.
Final Thoughts: Why Your Scale Blank Choice Matters
The scale blank might seem like a small detail, but it plays a crucial role in the accuracy and longevity of your weighing scale. Whether you’re a home cook, a business owner, or a lab technician, choosing the right material and maintaining it properly ensures reliable measurements every time.
Ready to upgrade your scale? Now that you know what to look for, you can make an informed decision and get the best performance out of your weighing device.
FAQs About Scale Blanks
Can I replace a damaged scale blank?
Yes, many manufacturers sell replacement blanks. Check compatibility before purchasing.
Are there antimicrobial scale blanks?
Some stainless steel blanks have antimicrobial coatings, ideal for medical or food industries.
How do I know if my scale blank is affecting accuracy?
If your scale gives inconsistent readings, inspect the blank for warping or damage.
Technology
Why You Need to Check Out the Socks5 Proxy List Wingate.me
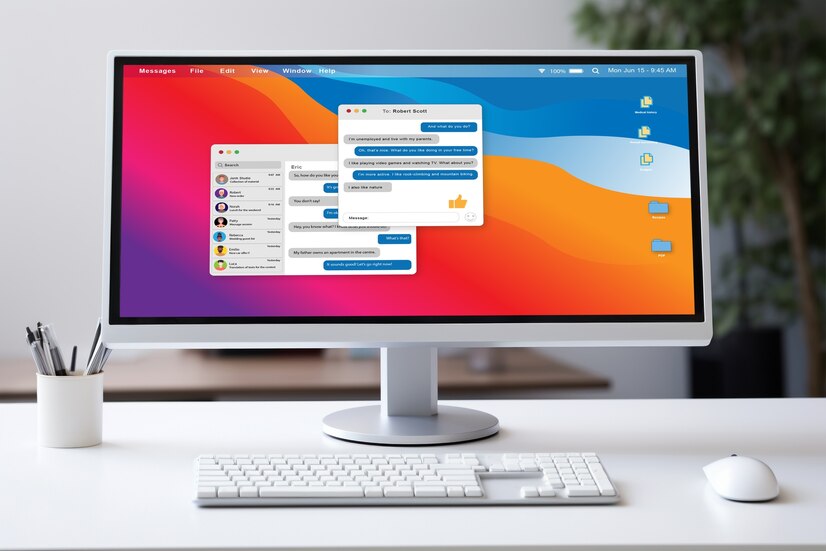
Looking to enhance your online security and privacy? Dive into the world of private proxies with Wingate.me’s Socks5 Proxy List! Whether you’re a seasoned web user or just starting out, this comprehensive list offers unparalleled protection and browsing freedom. Let’s explore why checking out Wingate.me’s Socks5 Proxy List is a game-changer for your online experience.
Navigation Menu
When it comes to navigating Wingate.me’s Socks5 Proxy List, the user-friendly interface makes finding what you need a breeze. The navigation menu is thoughtfully designed for easy access to various features and options, ensuring a seamless browsing experience. With clear labels and intuitive organization, you can quickly locate specific tools or settings without any hassle.
The menu layout allows users to navigate effortlessly between different sections of the proxy list, making it simple to switch between saved searches, repository files, latest commits, and more. Whether you’re a beginner or an advanced user, the navigation menu caters to all levels of expertise with its straightforward design and functionality.
By utilizing the navigation menu effectively, users can maximize their productivity and efficiency when exploring Wingate.me’s Socks5 Proxy List. Take advantage of this well-structured tool to streamline your browsing experience and unlock the full potential of private proxies for enhanced online security and privacy.
Use Saved Searches to Filter Your Results More Quickly
When browsing through a socks5 proxy list on Wingate.me, efficiency is key. One handy feature to streamline your search process is utilizing saved searches to filter results quickly. By saving specific search criteria such as location, speed, or anonymity level, you can access relevant proxies in just a few clicks.
This time-saving tool ensures that you don’t have to input the same filters repeatedly every time you revisit the site. Simply set your preferences once and let Wingate.me do the rest. Whether you’re looking for proxies for data scraping, geo-blocked content access, or cybersecurity purposes, using saved searches can help tailor your results to meet your exact needs.
With this functionality at your disposal, finding the perfect socks5 proxy becomes a breeze. Say goodbye to sifting through irrelevant options – optimize your search experience with saved searches on Wingate.me today!
Folders and Files
When it comes to navigating through the Socks5 Proxy List on Wingate.me, understanding the organization of folders and files is key. Each folder contains a specific category of proxies, neatly arranged for easy access. From streaming proxies to gaming proxies, you can find them all conveniently sorted within their respective folders.
Files within each folder provide detailed information about each proxy, including its speed, location, and anonymity level. This allows users to make informed decisions when selecting the right proxy for their needs. Whether you’re looking for fast speeds or reliable connections, exploring the various files in each folder can help you find the perfect match.
By utilizing the intuitive folder and file structure on Wingate.me’s Socks5 Proxy List, users can efficiently browse through different categories and options available to them. Easy navigation means less time searching and more time enjoying seamless proxy connections for all your online activities.
Latest Commit
Are you someone who always wants to stay up-to-date with the latest changes in your favorite projects? Well, at Wingate.me, we understand the importance of keeping track of the “Latest Commit” on our Socks5 Proxy List repository.
The “Latest Commit” feature allows you to see the most recent updates made to our proxy list, giving you real-time insights into any new additions or modifications. Whether it’s bug fixes, performance enhancements, or exciting new features, staying informed about the latest commit can help you make informed decisions when choosing proxies for your online activities.
By regularly checking out the latest commit section on Wingate.me’s platform, you can ensure that you are always using the most updated and optimized version of our socks5 proxy list. Stay ahead of the game and maximize your browsing experience by staying connected to our repository’s latest developments!
History
Have you ever wondered about the history of a website or online platform? The “History” section on Wingate.me provides valuable insights into past activities and changes made to the Socks5 proxy list. It’s like taking a trip down memory lane, seeing how the service has evolved over time.
By exploring this feature, users can track updates, modifications, and improvements implemented by Wingate.me. This historical perspective allows for a better understanding of how the platform has developed and adapted to meet user needs effectively.
Delving into the History section offers transparency and accountability as users can trace back any alterations or additions that have been made. It adds a layer of trust and reliability to the overall service provided by Wingate.me.
Repository Files Navigation
When it comes to navigating through repository files on Wingate.me, efficiency is key. The platform offers a seamless experience for users to locate and access specific files within their repositories effortlessly.
With intuitive search functionalities and organized file structures, finding the exact document you need becomes a breeze. Whether you’re looking for code snippets, configuration files, or any other data stored in your repository, Wingate.me streamlines the process.
By providing clear pathways to navigate through folders and subfolders, users can quickly drill down to the desired file without wasting time on unnecessary clicks. This user-friendly approach enhances productivity and ensures that developers can focus on their tasks rather than getting lost in complex directory structures.
Wingate.me’s repository files navigation feature simplifies file management and facilitates smooth collaboration among team members working on shared projects.
Releases
When it comes to the “Releases” section on Wingate.me’s Socks5 Proxy List, users can stay updated on the latest changes and improvements. This feature allows for easy tracking of when new versions or updates are launched, ensuring that you have access to the most current resources available.
By regularly checking the “Releases” tab, you can see any bug fixes, enhancements, or additional features that have been implemented into the proxy list. This transparency enables users to understand what modifications have been made and how they may impact their browsing experience.
Whether it’s a minor tweak or a significant upgrade, staying informed through the “Releases” section ensures that you are always aware of any advancements in Wingate.me’s Socks5 Proxy List. Stay ahead by keeping an eye on this section for any new developments that could benefit your proxy usage.
Packages
When it comes to exploring the functionalities and utilities of Wingate.me, the “Packages” feature stands out as a valuable tool for users. This section provides access to various pre-packaged sets of resources, tools, or configurations that can streamline your workflow and enhance your browsing experience.
By accessing packages through Wingate.me, users can easily integrate additional features or enhancements into their proxy setup without the hassle of manual configuration. Whether you’re looking for security add-ons, performance optimizations, or specialized tools, the Packages section offers a curated selection to choose from.
Each package is designed to cater to specific needs and preferences, allowing users to customize their proxy settings according to their requirements. From enhancing privacy protocols to optimizing connection speeds, these packages offer a convenient way to enhance your online activities effortlessly.
Exploring the Packages section on Wingate.me opens up a world of possibilities for maximizing the efficiency and effectiveness of your proxy usage. Unlock new capabilities and functionalities with just a few clicks in this dynamic repository of resources tailored for discerning users like yourself.
Footer
The footer section on a website might seem small, but it plays a significant role in user experience. It’s the final impression visitors have before leaving your site. The footer is like the cherry on top of a sundae – a finishing touch that ties everything together.
In the footer, you can find important links like contact information, privacy policies, terms and conditions, and social media icons for easy navigation. These elements help users feel more comfortable exploring your site and potentially converting into customers.
Design-wise, the footer can also showcase your brand’s personality through color schemes, fonts, and creative layouts. A well-designed footer not only looks professional but also enhances the overall aesthetics of your website.
Don’t underestimate the power of a well-crafted footer – it may be at the bottom of the page, but its impact on user engagement and satisfaction is anything but minor.
What Is A Socks5 Proxy?
Have you ever wondered how to enhance your online privacy and security while browsing the internet? Well, a Socks5 proxy might just be the solution you’re looking for.
In simple terms, a Socks5 proxy acts as an intermediary server between your device and the internet. When you connect to the internet through a Socks5 proxy, your IP address is masked, making it harder for websites to track your online activities.
Unlike traditional proxies, Socks5 proxies are highly versatile and can handle various types of traffic such as HTTP, HTTPS, FTP, and more. This flexibility makes them ideal for tasks like torrenting or accessing geo-restricted content.
Additionally, Socks5 proxies offer faster speeds and better performance compared to other proxy options. With its advanced features and benefits, using a Socks5 proxy can significantly improve your online experience by providing an extra layer of anonymity and security.
What Is Private Proxy Wingate.me?
Private Proxy Wingate.me offers a secure way to browse the internet anonymously. With this service, users can mask their IP addresses, enhancing privacy and security online. By utilizing private proxies, individuals can access websites without revealing their true location or identity.
Wingate.me’s private proxy service allows for seamless browsing without restrictions. Whether you’re accessing geo-blocked content or simply prioritizing your privacy, these proxies provide a reliable solution. Through encrypted connections, Wingate.me ensures that your data remains protected while surfing the web.
With Private Proxy Wingate.me, users can enjoy faster connection speeds and reduced latency compared to public proxies. This advantage is especially beneficial for activities like streaming or online gaming where performance matters. Additionally, Wingate.me offers dedicated customer support to assist with any technical issues that may arise when using their private proxy services.
In today’s digital landscape where privacy is paramount, Private Proxy Wingate.me stands out as a trusted provider of secure internet browsing solutions.
Types of Private Proxy Wingate.me
When it comes to private proxies, Wingate.me offers a variety of options to suit different needs and preferences.
One type of private proxy available on Wingate.me is the dedicated proxy. This type allocates a single IP address exclusively for your use, providing enhanced security and reliability for your online activities.
Another option is the rotating proxy offered by Wingate.me. With this type, you can automatically switch between multiple IP addresses at set intervals, allowing you to access diverse geo-locations and avoid detection.
Moreover, Wingate.me also provides shared proxies which are cost-effective solutions for those looking to mask their online identity without breaking the bank.
Each type of private proxy from Wingate.me caters to specific requirements, whether it’s individualized security measures or budget-friendly anonymity.
An Overview Of Wingate.me’s Socks5 Proxy List
At Wingate.me, the Socks5 proxy list is a powerful tool for enhancing your online security and privacy. This list provides users with access to a vast array of high-speed proxies that can help mask their IP addresses and encrypt their internet traffic. With the Socks5 protocol, you can enjoy fast and reliable connections while keeping your browsing activities anonymous.
The Socks5 proxy list offered by Wingate.me is regularly updated to ensure that users have access to the latest and most secure proxies available. Whether you’re looking to bypass geo-restrictions, protect your personal information from prying eyes, or simply enhance your online anonymity, this proxy list has got you covered.
By utilizing Wingate.me’s Socks5 proxy list, you can take control of your online experience and browse the web with confidence. Stay safe and secure while enjoying unrestricted access to content from around the globe.
The Benefits of Wingate.me’s Socks5 Proxy List
When it comes to online security and anonymity, Wingate.me’s Socks5 Proxy List offers a range of benefits that users can take advantage of. One key benefit is the enhanced level of privacy it provides by masking your IP address, making it harder for third parties to track your online activities.
Another advantage is the ability to bypass geo-restrictions and access content that may be blocked in your region. This can be particularly useful for streaming services or websites with regional restrictions.
Moreover, Wingate.me’s Socks5 Proxy List offers faster connection speeds compared to other proxy types, ensuring smooth browsing and minimal lag while maintaining a secure connection. This can be crucial for tasks that require high bandwidth or real-time data transfer.
Additionally, using Wingate.me’s Socks5 Proxy List adds an extra layer of security when connecting to public Wi-Fi networks, protecting your sensitive information from potential threats such as hackers or malicious software.
How To Set Up Wingate.me’s Socks5 Proxy?
Setting up Wingate.me’s Socks5 proxy is a straightforward process that allows you to enhance your online privacy and security. To begin, you first need to visit the Wingate.me website and sign up for an account. Once registered, navigate to the dashboard where you can access the list of available proxies.
Next, select the Socks5 proxy option from the menu and choose a server location that best suits your needs. After selecting a server, you will be provided with detailed instructions on how to configure your device or browser settings to connect to the chosen proxy.
Follow these instructions carefully, inputting the required information such as IP address, port number, username, and password. Once set up correctly, your internet traffic will be routed through Wingate.me’s secure Socks5 proxy server seamlessly.
By utilizing Wingate.me’s Socks5 proxy, you can enjoy enhanced anonymity and protection while browsing online.
Conclusion
In a world where online privacy and security are paramount, having access to a reliable socks5 proxy list like Wingate.me is essential. By utilizing Wingate.me’s private proxy services, you can enhance your online anonymity and protect your sensitive information from prying eyes.
With various types of private proxies available, including socks5 proxies, Wingate.me offers flexibility and customization to suit your specific needs. Whether you’re looking to bypass geo-restrictions, improve your browsing speed, or simply add an extra layer of security to your online activities, Wingate.me has got you covered.
Setting up Wingate.me’s socks5 proxy is quick and easy, allowing you to start benefiting from enhanced privacy and security in no time. Simply follow the straightforward instructions provided by Wingate.me to configure the socks5 proxy on your preferred device or browser.
Don’t compromise on your online safety – explore Wingate.me’s socks5 proxy list today and take control of your digital footprint. Stay protected, stay secure with Wingate.me!
Technology
Maple Juicer: Ultimate Guide to Tapping Nature’s Sweetest Nectar
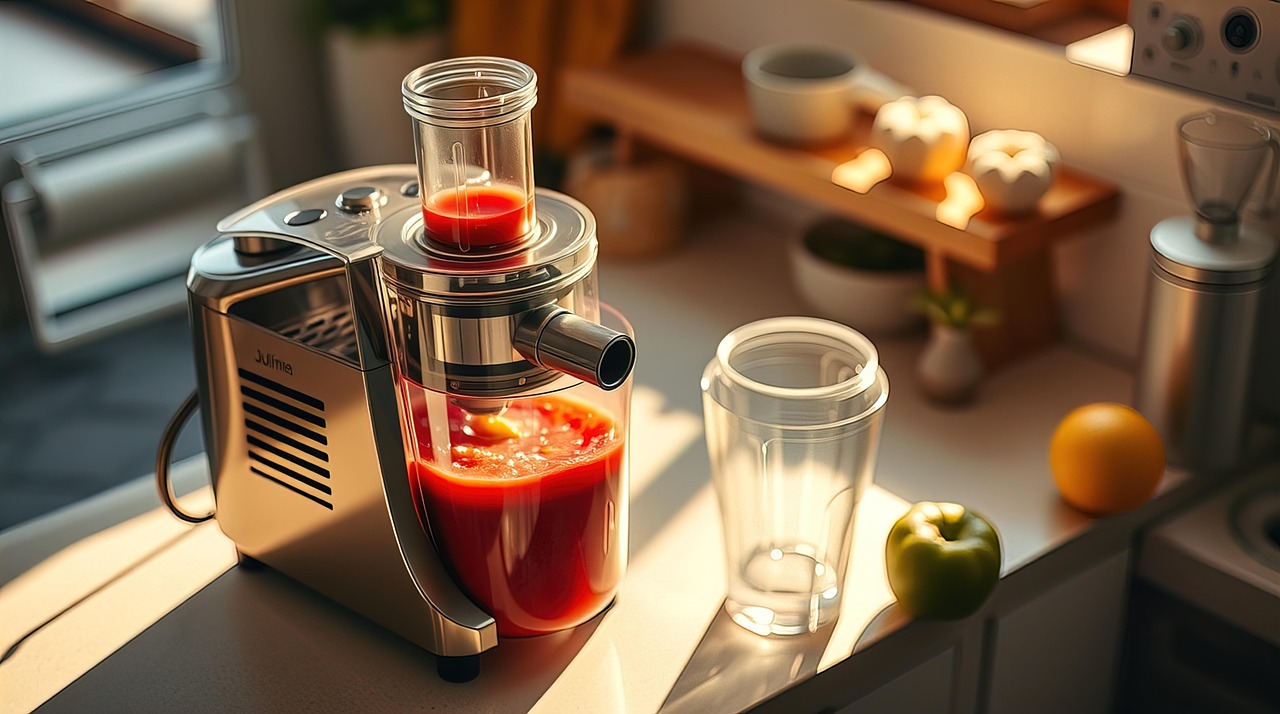
Have you ever wondered how that rich, golden maple syrup drizzled over your pancakes makes its way from tree to table? The secret lies in a simple yet ingenious tool—the maple juicer. Whether you’re a hobbyist, a homesteader, or a small-scale syrup producer, mastering the art of maple juicing can be incredibly rewarding.
In this guide, we’ll walk you through everything you need to know about maple juicers—from how they work to expert tips for maximizing your syrup yield. Let’s dive in!
What Is a Maple Juicer?
A maple juicer (or maple tap) is a device used to extract sap from sugar maple trees, which is then boiled down into delicious maple syrup. While the concept is centuries old, modern tools have made the process more efficient and accessible.
How Does It Work?
-
Tapping the Tree – A small hole is drilled into the maple tree.
-
Inserting the Spile – A spout (or “spile”) is placed into the hole to direct sap into a collection container.
-
Collecting the Sap – Sap flows out during warm days and cold nights (typically late winter to early spring).
-
Boiling Down – The collected sap is boiled to evaporate water, leaving pure maple syrup.
Types of Maple Juicers & Tapping Systems
Not all maple juicers are created equal. Here’s a breakdown of the most common types:
1. Traditional Bucket & Spile System
-
Best for: Small-scale hobbyists
-
How it works: Metal or plastic spiles drip sap into hanging buckets.
-
Pros: Low-cost, simple setup
-
Cons: Manual collection, risk of contamination
2. Tubing Systems with Vacuum Pumps
-
Best for: Medium to large-scale producers
-
How it works: A network of tubes connects multiple trees to a central collection tank, sometimes with a vacuum pump to increase yield.
-
Pros: Higher sap yield, less labor-intensive
-
Cons: More expensive, requires maintenance
3. Plastic Bag Systems
-
Best for: Beginners testing the waters
-
How it works: Disposable bags attach to spiles for easy sap collection.
-
Pros: Lightweight, no cleaning needed
-
Cons: Less durable, not ideal for high yields
How to Choose the Best Maple Juicer for Your Needs
Picking the right system depends on your goals, budget, and scale. Consider these factors:
✅ Budget – Bucket systems are cheapest, while tubing setups require investment.
✅ Number of Trees – Small operations (1-10 trees) can use buckets; larger setups benefit from tubing.
✅ Labor vs. Automation – Vacuum systems save time but need upkeep.
✅ Local Climate – Colder regions may need insulated tubing to prevent freezing.
Expert Tips for Maximizing Your Maple Sap Yield
Want to get the most out of your maple juicer? Follow these proven strategies:
1. Tap at the Right Time
-
Sap flows best when daytime temps are above freezing (40°F/4°C) and nights drop below freezing (20°F/-6°C).
-
In most regions, late February to early April is prime tapping season.
2. Choose Healthy, Mature Trees
-
Ideal trees are at least 10-12 inches in diameter (one tap per tree).
-
Larger trees (18+ inches) can handle two taps.
3. Drill the Perfect Hole
-
Use a sharp, clean drill bit (7/16″ or 5/16″ for smaller taps).
-
Drill at a slight upward angle (5-10°) to help sap flow.
4. Keep It Clean
-
Sanitize taps and buckets to prevent bacterial growth (a mix of 1-part bleach to 20-parts water works well).
-
Replace tubing every few years to avoid mold buildup.
5. Use a Vacuum System (If Possible)
-
Studies show vacuum-assisted tapping can increase sap yield by 50-100%!
Common Mistakes to Avoid
🚫 Tapping Too Early or Late – Miss the sap run, and you’ll get little to no yield.
🚫 Over-Tapping Small Trees – Damages the tree and reduces future sap production.
🚫 Poor Storage – Sap spoils quickly; refrigerate or boil within 24-48 hours.
🚫 Ignoring Weather Changes – A sudden warm spell can end the season early.
Real-World Success Story: From Backyard Hobby to Small Business
Meet Jake & Emily, a Vermont couple who started with five maple trees and a bucket system. After a few years of experimenting, they upgraded to a 300-tree tubing setup with a vacuum pump.
Their results?
-
Year 1: 5 trees → 1 gallon of syrup
-
Year 5: 300 trees → 75+ gallons of syrup (sold at local farmers’ markets)
Their secret? Starting small, learning from mistakes, and scaling wisely.
Final Thoughts: Is Maple Juicing Right for You?
Whether you’re a DIY enthusiast, a homesteader, or an aspiring syrup producer, tapping maple trees is a fulfilling (and delicious!) endeavor. With the right tools, timing, and techniques, you can turn your backyard into a mini syrup operation.
Ready to start? Grab a maple juicer, pick a healthy tree, and let nature’s sweetness flow!
-
Articles3 months ago
How Many Times Can You Regrow Green Onions
-
News10 months ago
Understanding HotLeaks: What You Need to Know
-
Fashion8 months ago
Opals in the USA: A Gemstone Transforming the Crystal Healing Market
-
Entertainment7 months ago
How to Use Snaptik: A Complete Guide to Download TikTok Videos
-
Technology1 year ago
The Wonders of Oh Em Gee Blog
-
Entertainment1 year ago
Bare it All: Unforgettable Skinny Dipping Stories Shared
-
Health1 year ago
Can You Smoke Shrooms? Exploring the Myths and Realities
-
Articles5 months ago
WHAT IS THE DIFFERENCE BETWEEN SEED GARLIC AND FOOD GARLIC?