Technology
Vessel Maintenance: Practices for Longevity and Performance
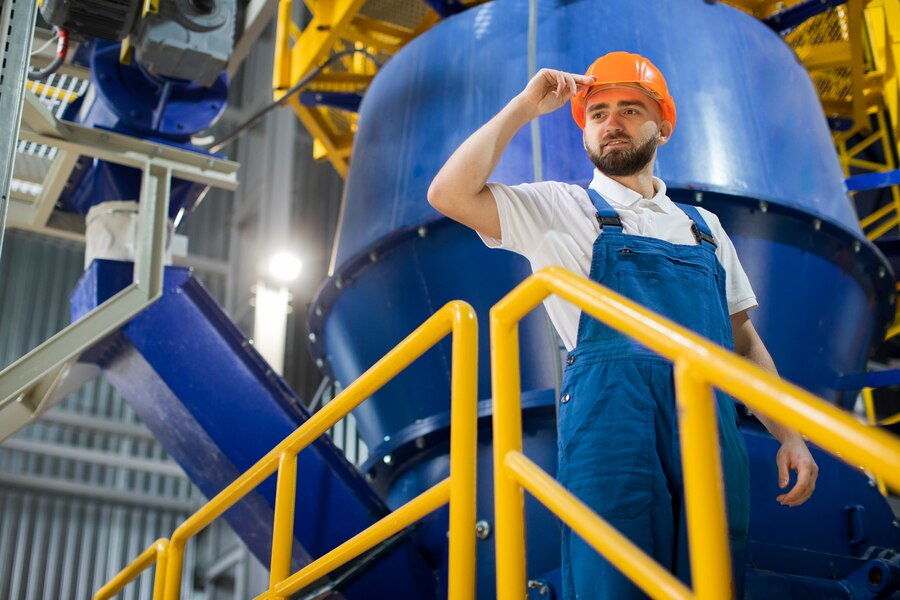
Vessel maintenance is a critical aspect of ensuring the longevity, performance, and safety of maritime vessels. Whether it’s a small recreational boat or a large commercial ship, regular maintenance prevents expensive repairs and downtime. This article delves into the importance of vessel maintenance, best practices, common mistakes to avoid, and the technological advancements shaping the industry. Let’s explore how proper maintenance can significantly extend the life of vessels, minimize operational disruptions, and enhance safety.
Understanding Vessel Maintenance
Vessel maintenance refers to the actions taken to keep a ship, boat, or any other floating vessel in optimal working condition. These actions typically include regular inspections, repairs, cleaning, and replacements of various vessel components. The goal of vessel maintenance is to ensure that the vessel remains seaworthy, operates efficiently, and adheres to safety and environmental regulations.
Types of Vessel Maintenance
There are several types of maintenance activities necessary to ensure the smooth operation of a vessel:
- Routine Maintenance: These are regular checks and tasks that need to be performed frequently, such as oil changes, engine checks, and cleaning of essential components.
- Corrective Maintenance: This type of maintenance is performed when a fault or failure is identified. Corrective actions are taken to restore the vessel’s functionality.
- Preventive Maintenance: This involves scheduled maintenance to prevent failure before it occurs. It includes replacing worn-out components, tightening bolts, and lubricating moving parts.
- Condition-Based Maintenance: Rather than following a strict schedule, condition-based maintenance involves monitoring the vessel’s systems and performing maintenance based on their performance or signs of wear.
- Overhaul Maintenance: Overhaul maintenance typically involves a complete inspection and reconditioning of major systems and components like engines or propulsion systems.
Why Vessel Maintenance is Important
The importance of regular vessel maintenance cannot be overstated. Here are several key reasons why maintaining a vessel is crucial:
1. Ensures Safety
The safety of the crew, passengers, and vessel itself is of utmost importance. Vessel maintenance ensures that all critical systems, such as navigation, propulsion, and communication systems, are functioning optimally. Neglecting maintenance could result in system failures, leading to dangerous situations at sea.
2. Prevents Expensive Repairs
Routine checks and maintenance can catch small issues before they turn into expensive, large-scale repairs. For instance, a minor leak can be fixed easily, but if left unchecked, it may lead to significant structural damage.
3. Improves Performance and Efficiency
Well-maintained vessels run more efficiently. For example, clean and lubricated engines consume less fuel and produce fewer emissions, contributing to lower operational costs and environmental impact.
4. Compliance with Regulations
Maritime vessels are subject to a range of regulatory requirements. Routine maintenance ensures that the vessel remains compliant with maritime laws and environmental regulations. Non-compliance can lead to fines or legal issues.
5. Increases Resale Value
Vessels that are properly maintained hold their value better than those that have been neglected. Regular maintenance records can increase the resale value, making it easier to sell the vessel when needed.
Key Areas of Vessel Maintenance
Understanding the areas that require attention is crucial for effective vessel maintenance. Below are some of the primary areas that need regular maintenance:
1. Engine and Propulsion Systems
Engines and propulsion systems are the heart of any vessel, and their maintenance is crucial to keep the vessel operational. Regularly check for oil leaks, corrosion, and wear and tear. Changing oil filters and checking coolant levels are vital to maintaining engine health.
2. Electrical Systems
Electrical components such as batteries, lights, navigational instruments, and communication systems need consistent checks. Poor battery performance can result in communication failures, while faulty wiring can lead to fires or system malfunctions.
3. Hull and Structural Integrity
The hull is the outer shell of the vessel, and maintaining its integrity is essential to prevent water ingress. Regular inspections for cracks, corrosion, and underwater damage are critical. Anti-fouling coatings should also be applied to prevent algae or barnacles from growing on the hull.
4. Fuel Systems
Inspecting the fuel system, including the tanks, pipes, and filters, is necessary to ensure there are no leaks or blockages. Contaminated fuel can cause engine problems and lead to costly repairs.
5. Navigation Systems
A vessel’s navigation system, including radar, GPS, and other instruments, must be maintained to ensure safe and accurate navigation. Regular updates to software and calibration of sensors are part of the maintenance routine.
6. Air Conditioning and Refrigeration
If a vessel has air conditioning or refrigeration systems, they should be regularly serviced. Keeping air filters clean, checking refrigerant levels, and inspecting the system for leaks are all essential tasks.
Common Vessel Maintenance Mistakes to Avoid
While vessel maintenance is critical, there are some common mistakes that many vessel owners and operators make. Being aware of these pitfalls can help you avoid them:
1. Skipping Regular Inspections
One of the most common mistakes is neglecting routine inspections. Even if everything appears to be functioning correctly, small issues can develop that may go unnoticed. Routine inspections help identify potential problems early.
2. Neglecting Engine Maintenance
The engine is one of the most important parts of a vessel. Skipping oil changes, fuel filter replacement, or neglecting coolant checks can lead to engine failures at sea, causing delays and significant repair costs.
3. Not Keeping Proper Records
Failure to maintain accurate maintenance records can be problematic, especially when it comes time to sell the vessel or demonstrate compliance with maritime regulations.
4. Using Low-Quality Parts
Cheap or subpar replacement parts may save money in the short term, but they can cause greater damage in the long run. Always opt for high-quality components that meet industry standards.
5. Ignoring Safety Systems
Life-saving equipment, such as life rafts, fire extinguishers, and first aid kits, should not be overlooked during maintenance routines. These systems must be checked regularly to ensure they are in working order.
Technological Advancements in Vessel Maintenance
Recent advancements in technology have made vessel maintenance more efficient and less costly. Some key innovations include:
1. Predictive Maintenance
Using sensors and IoT technology, predictive maintenance can anticipate failures before they occur. This technology monitors various vessel systems and predicts when they will need attention, allowing for timely interventions.
2. 3D Scanning and Modeling
3D scanning and modeling technology allow maintenance teams to create accurate digital twins of the vessel. This provides a clear view of the vessel’s structure and can help identify potential issues in hard-to-reach areas.
3. Drones and Robots
Drones and underwater robots are increasingly being used for inspections. These devices can access hard-to-reach areas like the hull or machinery spaces, making inspections safer and more thorough.
Vessel Maintenance Comparison Chart
Maintenance Area | Importance | Maintenance Frequency | Tools/Technologies Used |
---|---|---|---|
Engine & Propulsion | Vital for vessel movement and operation | Every 500-1,000 hours | Oil filters, engine diagnostics software |
Electrical Systems | Ensures communication and navigation | Quarterly or bi-annually | Battery testers, multimeter |
Hull & Structural | Prevents water ingress and damage | Annually, or after heavy weather | Anti-fouling paint, ultrasonic thickness testers |
Fuel Systems | Ensures efficient operation | Monthly | Fuel testers, pressure gauges |
Navigation Systems | Critical for safe navigation | Bi-annually | GPS software updates, calibration tools |
Air Conditioning | Comfort and operational efficiency | Annually | Refrigerant gauges, air filters |
Conclusion
Vessel maintenance is not just about ensuring that a vessel runs smoothly but also about protecting the investment, ensuring safety, and complying with regulations. By regularly inspecting critical systems, addressing issues promptly, and adopting new technologies, vessel owners and operators can keep their vessels in top condition for years to come. Regular maintenance can reduce the risk of breakdowns, improve efficiency, and extend the lifespan of the vessel.
As maritime technology continues to evolve, staying informed about the latest advancements in vessel maintenance is key to optimizing performance and minimizing costs. Remember, proactive maintenance today can prevent costly repairs tomorrow, ensuring your vessel remains safe, efficient, and ready for any journey.
Technology
SCMCompile: The Guide to Streamlining Your Supply Chain
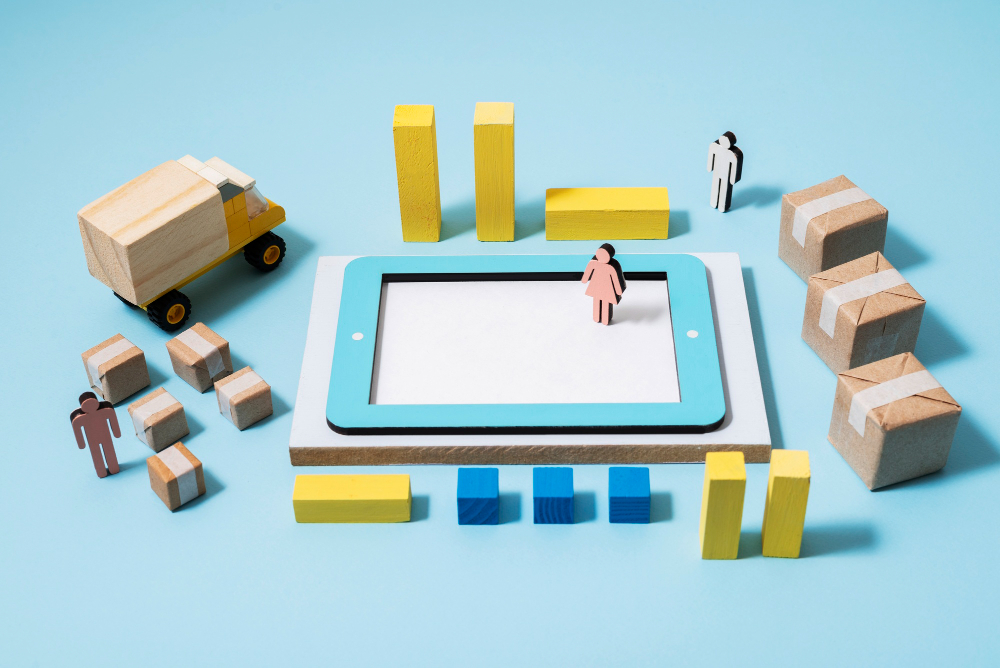
In today’s rapidly evolving business landscape, efficient supply chain management is no longer just an option; it’s a necessity. Companies that excel in optimizing their supply chain processes not only cut costs but also shorten delivery times, boost customer satisfaction, and ultimately gain a significant competitive advantage. One innovative tool making waves in this arena is SCMCompile.
But what exactly is SCMCompile, and how does it revolutionize supply chain operations? In this comprehensive guide, we’ll explore its standout features, notable benefits, real-world applications, and effective strategies for successful implementation.
What Is SCMCompile?
SCMCompile is a cutting-edge supply chain management optimization tool designed to streamline and enhance the workflows of supply chains through automation and intelligent analytics. Here’s what SCMCompile can do for your business:
-
Automate Procurement & Inventory Management: Say goodbye to manual tracking.
-
Optimize Logistics & Distribution: Find the fastest routes with minimal costs.
-
Slash Operational Costs: Leverage data-driven insights to improve efficiency.
-
Enhance Supplier Collaboration: Foster better communication with vendors.
What sets SCMCompile apart from traditional SCM software is its integration of AI and machine learning capabilities. These technologies empower businesses to predict demand fluctuations, identify inefficiencies, and make real-time adjustments.
Why SCMCompile Matters for Modern Supply Chains
Today’s supply chains are fraught with challenges, including:
-
Demand Volatility: Sudden shifts in market demand disrupt planning.
-
Supplier Delays: Geopolitical issues and logistics bottlenecks cause unforeseen delays.
-
Cost Pressures: Increasing fuel and labor costs squeeze profit margins.
SCMCompile addresses these challenges head-on through:
-
Predictive Analytics: Forecast demand accurately using historical data and trends.
-
Automated Replenishment: Automatically triggers orders when inventory dips below a defined threshold.
-
Route Optimization: Finds the most efficient shipping routes for cost savings.
Real-World Impact: Retail Giant Reduces Costs by 15%
For instance, a leading retail chain adopted SCMCompile and achieved impressive results:
-
15% reduction in excess inventory
-
20% faster order fulfillment
-
10% lower logistics costs
These results showcase how innovative tools like SCMCompile can lead to significant ROI.
Key Features of SCMCompile
-
AI-Driven Demand Forecasting:
-
Leverages past sales, seasonality, and market indicators for accurate demand predictions.
-
Automatically adjusts inventory levels to prevent stockouts and overstock situations.
-
-
Smart Procurement Automation:
-
Automates negotiations with suppliers to secure bulk discounts.
-
Flags potential disruptions, like adverse weather, to manage expectations.
-
-
Real-Time Logistics Optimization:
-
Integrates with GPS and traffic data to suggest immediate route adjustments.
-
Recommends alternative carriers if disruptions occur.
-
-
Supplier Performance Tracking:
-
Monitors vendor performance based on delivery speed, product quality, and pricing.
-
Suggests alternative suppliers if a vendor’s performance dips below standards.
-
-
Blockchain for Supply Chain Transparency:
-
Ensures traceability in compliance-heavy industries such as pharmaceuticals and food.
-
How to Successfully Implement SCMCompile
Step 1: Assess Your Current Supply Chain
-
Identify and analyze bottlenecks (e.g., slow supplier response times).
-
Define Key Performance Indicators (KPIs) such as order cycle time and fill rate.
Step 2: Integrate with Existing Systems
-
Ensure compatibility with your current ERP (like SAP or Oracle), Warehouse Management Systems (WMS), and Transportation Management Systems (TMS).
Step 3: Train Your Team
-
Conduct workshops to help staff interpret AI-driven recommendations.
-
Create incentives to encourage team members to adopt the new system.
Step 4: Monitor & Optimize
-
Regularly track key performance metrics and refine algorithms as more data becomes available.
Addressing Potential Challenges
While implementing new technology, businesses may face challenges such as:
-
Resistance to Change: Engage your teams early to promote buy-in.
-
Data Quality Issues: Cleanse outdated data before migrating to the new system.
-
High Initial Costs: Initiate a pilot program to demonstrate potential ROI before full implementation.
The Future of SCMCompile and Supply Chain Technology
Experts predict that the future will see further integration of technologies like AI, IoT, and blockchain reshaping SCM. Upcoming trends include:
-
Autonomous Logistics: Think self-driving trucks and drone deliveries.
-
Hyper-Personalized Supply Chains: Custom packaging and swift last-mile delivery solutions.
-
Sustainability Analytics: Monitoring carbon footprints and promoting eco-friendly practices.
Final Thoughts: Is SCMCompile Right for Your Business?
If your organization struggles with issues such as:
-
Excess inventory costs
-
Late shipments
-
Supplier reliability challenges
Then SCMCompile could be a transformative solution for your supply chain management. Start with a trial, assess the improvements, and gradually scale the implementation.
Pro Tip: Pair SCMCompile with a robust change management strategy to maximize adoption and achieve standout results.
Technology
A Guide to Planning a Multilingual Online Event
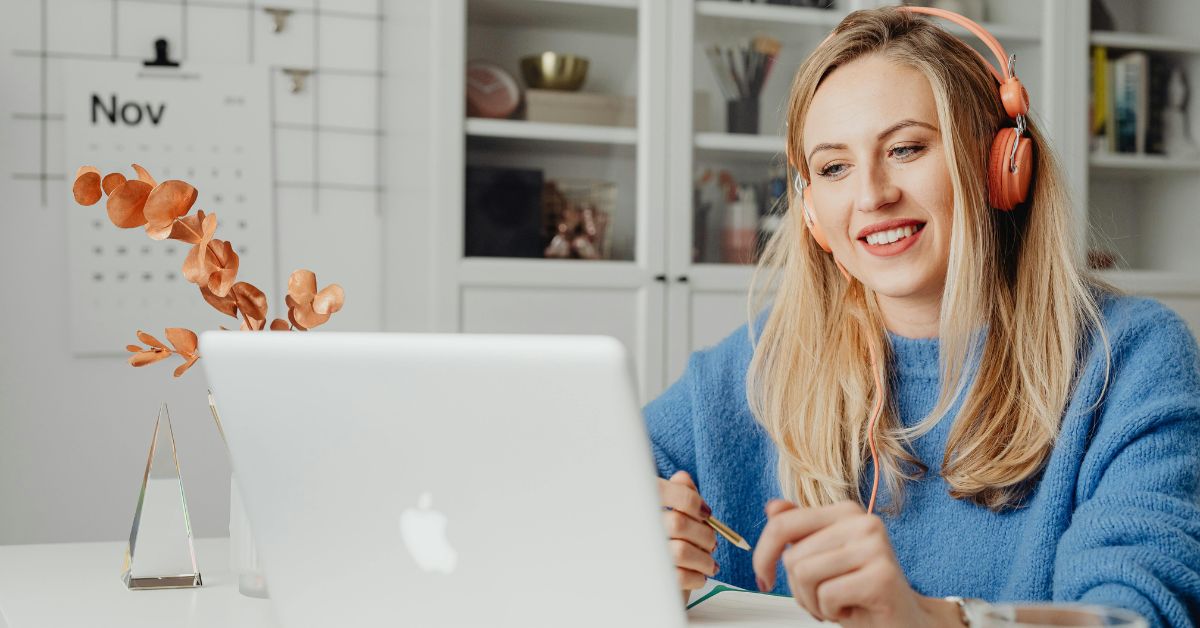
When people connect from different parts of the world, it’s only natural that they don’t all speak the same language. Still, it’s increasingly common for them to share the same screen. The rise of global meetings, digital conferences, product launches, and hybrid events is removing physical barriers—but it’s also challenging us to rethink how we communicate. A stable internet connection and a user-friendly platform are no longer enough. Effective communication in remote events now requires considering what each participant hears, sees, and understands—regardless of the language they think in.
Why Language Decisions Should Be Made Early
One of the most common mistakes in planning virtual events is leaving the language component until the end. In reality, language should be considered from the very first draft of the event. This doesn’t just mean deciding whether to include subtitles, live interpretation, or voiceover—it means understanding the expectations of your audience, their roles, and how they’ll interact.
One thing truly global events have in common is that they view their audience as a diverse group with varying levels of language fluency—and they actively work to include everyone in the experience. This is achieved by combining a variety of tools and services that make up the current landscape of language solutions. There’s no one-size-fits-all approach. It’s about identifying the best format for each type of content, determining what’s technically feasible, and ensuring a consistent, high-quality experience for all participants.
When to Use Subtitles, Interpretation, or Voiceover
Not every strategy works for every event. The key is selecting the right tool for the type of communication you’re delivering. For events with single speakers and linear presentations, simultaneous interpretation is often the best choice. It allows each attendee to choose their preferred audio channel and listen in real time in their own language. However, this setup requires reliable technical infrastructure, professional interpreters, and pre-event coordination with speakers.
For more visual events—or ones where accuracy is critical, such as technical product launches or training sessions—real-time subtitles might be a better fit. They support viewers who partially understand the original language and enhance accessibility for people with hearing impairments. In these cases, fast, clear, and accurate transcription is essential.
Voiceover, though less common for live events, can be valuable for pre-recorded webinars or content that will be shared post-event. Its main advantage is delivering a fully localized experience, though it requires more time and editing. Some companies even combine formats—offering live interpretation during the event and a dubbed version for on-demand distribution later.
The Limits of Machine Translation for Live Events
AI-powered tools have greatly expanded the availability of automatic translation and subtitling. While they can be helpful in informal settings, they still have major limitations when it comes to quality, nuance, and context. In most professional or corporate settings, automated translation should be used with caution.
Human input is still crucial for ensuring accuracy and adapting tone, cultural references, and expressions. A trained interpreter can convey intent and emotion in ways that algorithms simply can’t—at least not yet. So while technology can assist, suggest, or accelerate certain tasks, it does not replace the need for thoughtful planning and expert curation in serious multilingual events.
Technical implementation also requires attention. Choosing a streaming or video conferencing platform that supports multiple audio tracks, interpretation channels, or synchronized subtitles is not a trivial decision. Specialized tools exist for this, and testing them well in advance is highly recommended.
Preparing the Tech Team and Interpreters
Beyond technology, events are still a human experience. That means the team involved needs to be properly prepared. If your event includes live interpreters, it’s essential to provide them with all presentation materials in advance, clearly define their shifts, and ensure they have an appropriate acoustic and technical setup. The same goes for moderators and presenters: they must know how to activate multilingual features, guide the audience, and answer common participant questions.
In large events or ones with multiple simultaneous sessions, it can be helpful to assign a dedicated language coordination manager. This person ensures that each language channel is running smoothly and can assist attendees facing technical issues. Their role becomes even more valuable when the audience includes participants with limited digital literacy or accessibility challenges.
Multilingual Virtual Event Planning Checklist
Planning a multilingual online event can be complex—but much easier when you follow a clear roadmap. This checklist offers a foundational guide to help you deliver a smooth, professional experience:
Before the event:
- Define the primary languages and delivery methods (audio, subtitles, voiceover)
- Choose experienced providers for interpretation, subtitling, or dubbing
- Confirm that your platform supports multiple audio tracks and/or subtitles
- Train the technical team and moderators on multilingual features
- Run a full event rehearsal including interpretation or subtitling
- Send interpreters all relevant materials: presentations, glossaries, agenda
During the event:
- Activate and test language channels before going live
- Guide attendees on how to access their preferred language
- Set up a tech support channel to handle attendee questions
- Monitor audio quality across all channels
- Coordinate interpreter transitions for long sessions
After the event:
- Evaluate the quality of interpretation or subtitles
- Collect feedback from attendees on their language experience
- Use feedback to improve future events
- Prepare edited versions with dubbing or subtitles for post-event sharing
- Publicly thank your language and technical teams
Beyond Language, It’s About What You Share
Thinking in multiple languages isn’t just a nice-to-have—it’s a way to design more inclusive events where ideas aren’t lost in translation but flow freely. The strength of a global audience lies in its diversity, and each language is a doorway into that shared conversation. Planning with this in mind can be the difference between a meeting that’s simply heard—and one that’s truly understood.
Technology
The Scale Blank: How to choose Perfect One for Your Needs
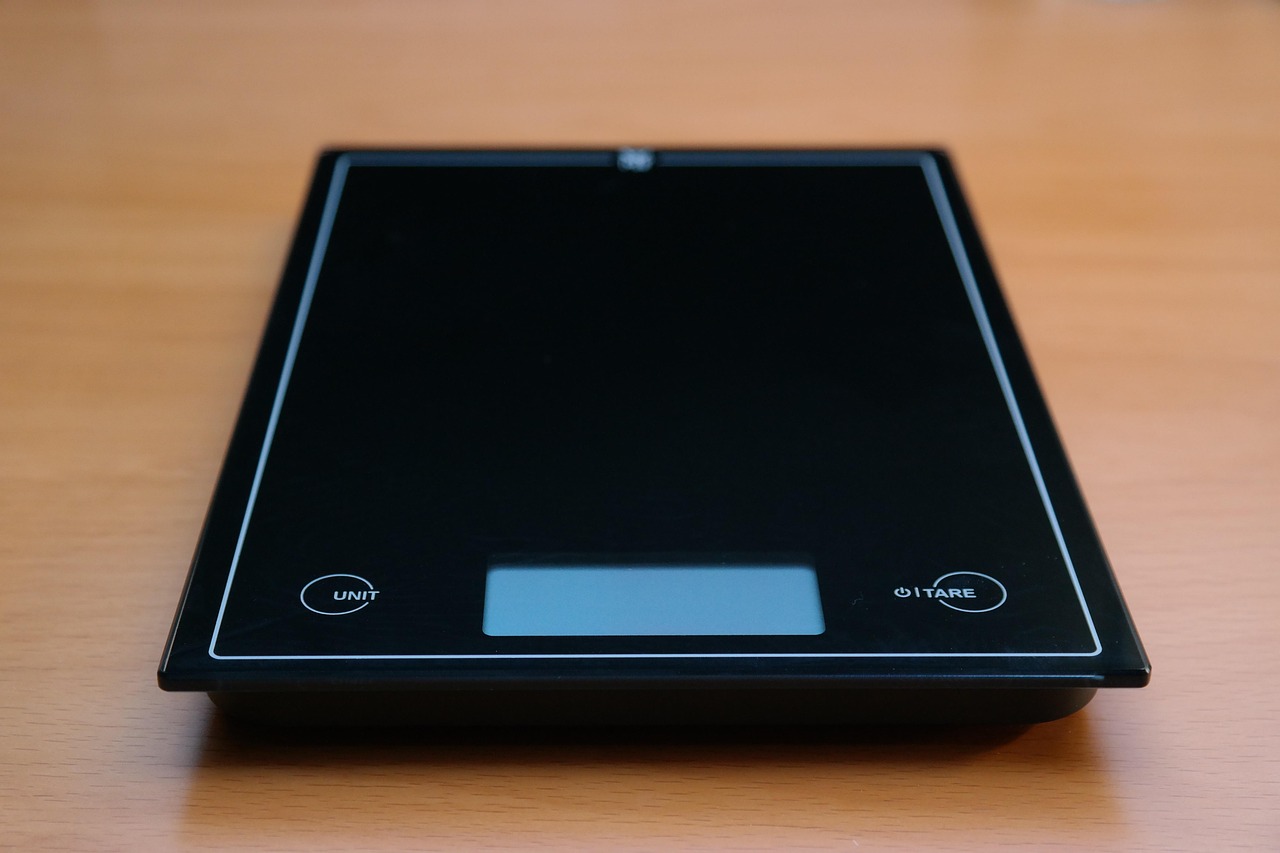
Have you ever wondered why some kitchen scales perform flawlessly while others fail within months? The secret often lies in an overlooked component—the scale blank. Whether you’re a home cook, a professional chef, or a business owner, choosing the right scale blank can make all the difference in accuracy, durability, and performance.
In this guide, we’ll break down everything you need to know about scale blanks—what they are, why they matter, and how to pick the best one for your needs.
What Is a Scale Blank?
A scale blank is the foundational platform of a weighing scale where items are placed for measurement. It’s the flat surface (usually made of stainless steel, glass, or plastic) that interacts directly with whatever you’re weighing.
Why Does It Matter?
-
Accuracy: A poorly designed blank can flex or warp, leading to incorrect readings.
-
Durability: The material determines how well it resists scratches, stains, and wear.
-
Hygiene: Some blanks are easier to clean, making them ideal for food or medical use.
Types of Scale Blanks: Pros and Cons
Not all scale blanks are created equal. Here’s a breakdown of the most common types:
1. Stainless Steel Blanks
✅ Pros:
-
Highly durable and resistant to corrosion
-
Easy to clean (ideal for kitchens and labs)
-
Provides a stable weighing surface
❌ Cons:
-
Can be slippery for lightweight items
-
Prone to fingerprints and smudges
Best for: Commercial kitchens, laboratories, and industrial settings.
2. Glass Blanks
✅ Pros:
-
Sleek, modern appearance
-
Easy to wipe clean
-
Doesn’t absorb odors or stains
❌ Cons:
-
Fragile—can crack under heavy weight
-
Slippery for certain items
Best for: Home kitchens, bakeries, and retail displays.
3. Plastic Blanks
✅ Pros:
-
Lightweight and affordable
-
Resistant to minor impacts
-
Non-slip surface in some models
❌ Cons:
-
Less durable over time
-
Can absorb stains and odors
Best for: Budget-friendly home scales or portable options.
How to Choose the Right Scale Blank
Picking the best scale blank depends on your specific needs. Here’s what to consider:
1. Intended Use
-
Cooking/Baking? Stainless steel or glass for easy cleaning.
-
Industrial Weighing? Reinforced stainless steel for durability.
-
Portable Scale? Lightweight plastic for convenience.
2. Weight Capacity
-
Small kitchen scales (1–10 lbs): Glass or plastic.
-
Heavy-duty scales (50+ lbs): Thick stainless steel.
3. Maintenance & Cleaning
-
Stainless steel: Wipe with a damp cloth.
-
Glass: Use glass cleaner for shine.
-
Plastic: Avoid abrasive cleaners to prevent scratches.
4. Anti-Slip Features
Some blanks have textured surfaces or rubberized edges to prevent items from sliding off.
5. Budget
-
Premium: Stainless steel
-
Mid-range: Tempered glass
-
Budget-friendly: High-quality plastic
Real-World Examples: Where Scale Blanks Make a Difference
Example 1: Bakery Business
A bakery switched from plastic to stainless steel blanks and saw fewer inaccuracies in dough measurements, leading to more consistent products.
Example 2: Home Cooks
A home chef using a glass scale blank found it easier to clean after measuring sticky ingredients like honey or syrup.
Example 3: Lab Environments
A research lab using high-grade stainless steel blanks avoided corrosion from chemical spills, ensuring long-term reliability.
Expert Tips for Maintaining Your Scale Blank
To extend the lifespan of your scale blank:
✔ Clean regularly—avoid buildup of debris.
✔ Avoid overloading—stick to the maximum weight limit.
✔ Store properly—keep in a dry place to prevent rust (for metal blanks).
✔ Check for damage—cracks or warping can affect accuracy.
Final Thoughts: Why Your Scale Blank Choice Matters
The scale blank might seem like a small detail, but it plays a crucial role in the accuracy and longevity of your weighing scale. Whether you’re a home cook, a business owner, or a lab technician, choosing the right material and maintaining it properly ensures reliable measurements every time.
Ready to upgrade your scale? Now that you know what to look for, you can make an informed decision and get the best performance out of your weighing device.
FAQs About Scale Blanks
Can I replace a damaged scale blank?
Yes, many manufacturers sell replacement blanks. Check compatibility before purchasing.
Are there antimicrobial scale blanks?
Some stainless steel blanks have antimicrobial coatings, ideal for medical or food industries.
How do I know if my scale blank is affecting accuracy?
If your scale gives inconsistent readings, inspect the blank for warping or damage.
-
Articles5 months ago
How Many Times Can You Regrow Green Onions
-
Fashion10 months ago
Opals in the USA: A Gemstone Transforming the Crystal Healing Market
-
News1 year ago
Understanding HotLeaks: What You Need to Know
-
Entertainment9 months ago
How to Use Snaptik: A Complete Guide to Download TikTok Videos
-
Technology1 year ago
The Wonders of Oh Em Gee Blog
-
Entertainment1 year ago
Bare it All: Unforgettable Skinny Dipping Stories Shared
-
Health1 year ago
Can You Smoke Shrooms? Exploring the Myths and Realities
-
Busniess5 months ago
Why Is Business Part of Science: Strategy, Innovation Explained