Technology
CNC Swiss Lathe vs CNC Router: Which One Costs More?
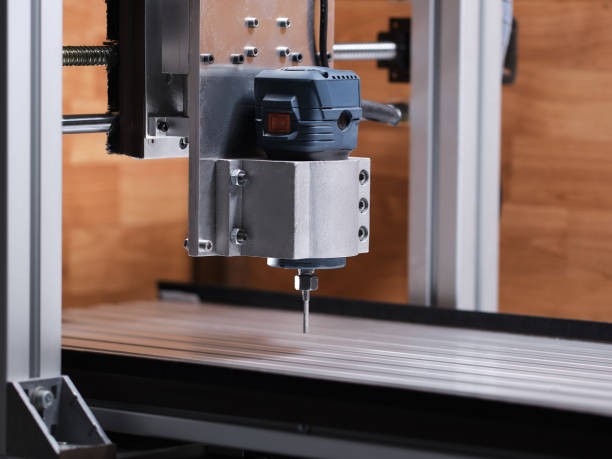
Meta Description: Which CNC machine offers better value for your investment: a Swiss Lathe or a Router? Dive into our comprehensive guide to uncover the cost differences and determine which suits your production needs best.
When investing in machining equipment, it’s vital to understand the differences between various tools to make the right decision. The CNC Swiss Lathe and CNC Router are two powerful machines that have become staples in precision CNC services. Both are known for their ability to produce highly accurate components, but they are designed for different types of operations. Therefore, given their various capabilities and uses, it’s not surprising that their costs also differ.
But how do you determine which one is the more expensive option? In this article, we will compare the costs associated with both machines. By exploring their features, productivity, and overall value, you’ll better understand which machine might be the better investment for your specific needs and budget.
What Is a CNC Swiss Lathe?
close up image of CNC swiss lathe for precision manufacturing
The CNC Swiss Lathe is a specialized type of lathe that produces small, intricate parts with unparalleled precision. The machine was originally developed in Switzerland for the watchmaking industry and has since evolved into a crucial tool in various high-precision fields, including medical device manufacturing, aerospace, and electronics.
How It Works
The CNC Swiss Lathe operates differently from traditional lathes. In a standard lathe, the workpiece remains stationary while the cutting tools move across it. In contrast, a Swiss Lathe feeds the workpiece through a guide bushing, holding it tightly as the cutting tools perform their tasks. This setup allows the workpiece to be machined very close to the point of support, reducing deflection and enabling the production of precise and intricate parts.
One of the standout features of the CNC Swiss Lathe is its ability to conduct multiple operations in a single setup. The machine can execute turning, milling, drilling, and even threading simultaneously, thanks to its numerous axes and live tooling capabilities. This enhances productivity and ensures the machine maintains consistent accuracy, often achieving tolerances as tight as a few microns.
What Is a CNC Router?
table legs carving with multi heads of CNC router machine
A CNC Router is a versatile, computer-controlled cutting machine that can carve, cut, and shape various materials, including wood, plastics, metals, and composites. Unlike the CNC Swiss Lathe, which specializes in the precision turning of small parts, the CNC Router excels in handling larger workpieces and producing highly accurate complex shapes. Industries such as woodworking, metalworking, signage, and furniture manufacturing heavily rely on CNC Routers for their production processes.
How It Works
The CNC router operates on a principle similar to other CNC machines, where computer-aided design (CAD) software generates the design, and computer-aided manufacturing (CAM) software translates that design into machine code. This code instructs the router to move its cutting tools to achieve the desired shape.
A typical CNC Router consists of a work table, a spindle (the motor that drives the cutting tool), and multiple axes—usually three, but sometimes more in advanced models. The router’s spindle moves along the X, Y, and Z axes to precisely carve out intricate designs or cut through the material. The router can accommodate various cutting tools, from end mills to drill bits, allowing it to perform multiple tasks, including cutting, drilling, engraving, and milling.
Cost Considerations for CNC Swiss Lathe vs CNC Router
Check the cost considerations for both precision CNC machines below:
CNC Swiss Lathe
When considering cost, the CNC Swiss Lathe generally falls on the higher end of the spectrum. The initial investment for these machines ranges depending on the model, brand, and available axes and tooling options. However, this high upfront cost often pays off in industries where precision, speed, and reliability are crucial.
Ongoing costs, such as maintenance, tooling, and operator training, also contribute to the overall expense. Due to the machine’s complexity, operators require specialized training to utilize its capabilities, which adds to the overall cost. Despite these costs, the CNC Swiss Lathe can deliver a substantial return on investment, especially in high-volume production where precision and consistency are crucial.
CNC Router
CNC Routers generally have a lower entry cost than CNC Swiss Lathes, making them accessible to various businesses, including small workshops. Prices for CNC Routers can vary widely based on the machine’s size, capabilities, and the materials it can handle. Basic models are usually less expensive, while more advanced models with larger work areas, higher power spindles, and additional features come at a much higher price.
Beyond the initial purchase price, other costs include tooling, maintenance, and potentially upgrading the software or hardware to keep the machine performing at its best. Operators also need training, though it may not be as extensive as the training required for CNC Swiss Lathes. Similarly, the return on investment for a CNC Router can be substantial. This is because its capability to handle multiple tasks in a single setup saves time and cuts labor costs, thus making it a cost-effective choice for many businesses.
Here’s a concise comparison table for the CNC Swiss Lathe and CNC Router highlighting the cost considerations:
Aspect | CNC Swiss Lathe | CNC Router |
Machine initial cost | High, as it ranges from $150,000 up to $500,000 or more, depending on the model | Less than CNC Swiss Lathe as it ranges from $50,000 to $150,000+, also depending on the model |
Ongoing Costs | Maintenance, tooling, operator training | Tooling, maintenance, software/hardware upgrades |
Training Requirements | Specialized and extensive | Basic to moderate |
Return on Investment | Significant in high-volume production | Substantial in versatile application |
Precision | High | Moderate to High |
CNC Swiss Lathe vs CNC Router: Which One Is Better in Productivity?
precision metal components made with CNC machines for industrial applications
When comparing the productivity of a CNC Swiss Lathe vs a CNC Router, it’s essential to understand that productivity can vary greatly depending on the specific application, the type of workpiece, and the required level of precision.
Check the details on the productivity of both machines below:
Productivity of a CNC Swiss Lathe
The CNC Swiss Lathe shines in tasks where precision and small-part production are paramount. One of the key factors contributing to the CNC Swiss Lathe’s productivity is its multi-axis capability. With the ability to work on multiple axes simultaneously, the machine can execute complex machining tasks without repositioning the workpiece. In a high-volume production, the CNC Swiss Lathe can produce thousands of identical parts with minimal variation, ensuring that each piece meets the required specifications without requiring extensive quality checks or rework.
However, the CNC Swiss Lathe’s focus on precision and complexity also means that it may not be the fastest option for simpler tasks. If your production needs involve larger parts or less intricate designs, the time and effort required to set up and run a Swiss Lathe might outweigh the benefits. Additionally, the machine’s complexity often necessitates specialized training for operators, which could slow down productivity during the initial stages of operation.
Productivity of a CNC Router
On the other hand, the CNC Router excels in scenarios where versatility and the ability to handle larger workpieces are key. Its design allows for rapid material removal and the ability to cut, carve, and shape a wide range of materials with relative ease. The CNC Router’s capacity to switch between different tools automatically during a job enhances its productivity. For instance, in woodworking, a CNC Router can cut the main shape of a piece, switch to a different tool to carve intricate details, and then drill holes—all in a single setup. This, in turn, increases overall output. In addition, CNC routers typically have larger work areas, allowing for processing bigger pieces of material in one go, thus enhancing productivity.
While CNC Routers are generally faster and more versatile than Swiss Lathes, they may not match the precision of a Swiss Lathe for extremely detailed or small-scale work. However, for most applications requiring speed, versatility, and considerable accuracy, a CNC Router is often the more productive option.
How to Choose the Right Machine for Your Productivity Needs
When deciding which machine is better in terms of productivity, consider the nature of the work you’ll be doing. Suppose your production requires the creation of small, highly intricate parts with tight tolerances. In that case, the CNC Swiss Lathe’s ability to deliver precision and consistency at high volumes makes it the superior choice. However, the CNC Router may offer better overall productivity if your needs lean towards versatility and faster production times.
Conclusion
Choosing between a CNC Swiss Lathe and a CNC Router ultimately depends on your manufacturing needs. The CNC Swiss Lathe produces small, intricate parts with unmatched precision. However, this precision comes at a higher cost and requires specialized training. On the other hand, the CNC Router offers greater versatility and speed, making it the better option for handling larger workpieces and various materials. Your choice between the two should be guided by whether precision or versatility better serves your production needs.
You can transform your manufacturing capabilities with Zintilon’s CNC precision machining services. Whether you’re seeking precision with a CNC Swiss Lathe or versatility with a CNC Router, we have the expertise to guide you in making the best investment for your business. Don’t wait; reach out today and discover how we can help you achieve superior productivity.
Technology
SCMCompile: The Guide to Streamlining Your Supply Chain
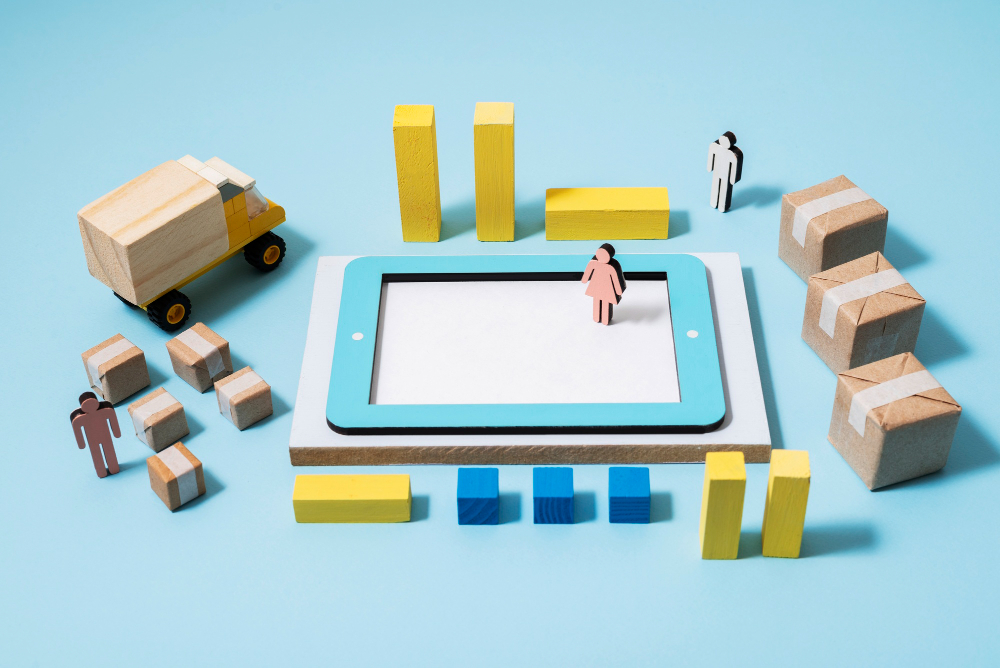
In today’s rapidly evolving business landscape, efficient supply chain management is no longer just an option; it’s a necessity. Companies that excel in optimizing their supply chain processes not only cut costs but also shorten delivery times, boost customer satisfaction, and ultimately gain a significant competitive advantage. One innovative tool making waves in this arena is SCMCompile.
But what exactly is SCMCompile, and how does it revolutionize supply chain operations? In this comprehensive guide, we’ll explore its standout features, notable benefits, real-world applications, and effective strategies for successful implementation.
What Is SCMCompile?
SCMCompile is a cutting-edge supply chain management optimization tool designed to streamline and enhance the workflows of supply chains through automation and intelligent analytics. Here’s what SCMCompile can do for your business:
-
Automate Procurement & Inventory Management: Say goodbye to manual tracking.
-
Optimize Logistics & Distribution: Find the fastest routes with minimal costs.
-
Slash Operational Costs: Leverage data-driven insights to improve efficiency.
-
Enhance Supplier Collaboration: Foster better communication with vendors.
What sets SCMCompile apart from traditional SCM software is its integration of AI and machine learning capabilities. These technologies empower businesses to predict demand fluctuations, identify inefficiencies, and make real-time adjustments.
Why SCMCompile Matters for Modern Supply Chains
Today’s supply chains are fraught with challenges, including:
-
Demand Volatility: Sudden shifts in market demand disrupt planning.
-
Supplier Delays: Geopolitical issues and logistics bottlenecks cause unforeseen delays.
-
Cost Pressures: Increasing fuel and labor costs squeeze profit margins.
SCMCompile addresses these challenges head-on through:
-
Predictive Analytics: Forecast demand accurately using historical data and trends.
-
Automated Replenishment: Automatically triggers orders when inventory dips below a defined threshold.
-
Route Optimization: Finds the most efficient shipping routes for cost savings.
Real-World Impact: Retail Giant Reduces Costs by 15%
For instance, a leading retail chain adopted SCMCompile and achieved impressive results:
-
15% reduction in excess inventory
-
20% faster order fulfillment
-
10% lower logistics costs
These results showcase how innovative tools like SCMCompile can lead to significant ROI.
Key Features of SCMCompile
-
AI-Driven Demand Forecasting:
-
Leverages past sales, seasonality, and market indicators for accurate demand predictions.
-
Automatically adjusts inventory levels to prevent stockouts and overstock situations.
-
-
Smart Procurement Automation:
-
Automates negotiations with suppliers to secure bulk discounts.
-
Flags potential disruptions, like adverse weather, to manage expectations.
-
-
Real-Time Logistics Optimization:
-
Integrates with GPS and traffic data to suggest immediate route adjustments.
-
Recommends alternative carriers if disruptions occur.
-
-
Supplier Performance Tracking:
-
Monitors vendor performance based on delivery speed, product quality, and pricing.
-
Suggests alternative suppliers if a vendor’s performance dips below standards.
-
-
Blockchain for Supply Chain Transparency:
-
Ensures traceability in compliance-heavy industries such as pharmaceuticals and food.
-
How to Successfully Implement SCMCompile
Step 1: Assess Your Current Supply Chain
-
Identify and analyze bottlenecks (e.g., slow supplier response times).
-
Define Key Performance Indicators (KPIs) such as order cycle time and fill rate.
Step 2: Integrate with Existing Systems
-
Ensure compatibility with your current ERP (like SAP or Oracle), Warehouse Management Systems (WMS), and Transportation Management Systems (TMS).
Step 3: Train Your Team
-
Conduct workshops to help staff interpret AI-driven recommendations.
-
Create incentives to encourage team members to adopt the new system.
Step 4: Monitor & Optimize
-
Regularly track key performance metrics and refine algorithms as more data becomes available.
Addressing Potential Challenges
While implementing new technology, businesses may face challenges such as:
-
Resistance to Change: Engage your teams early to promote buy-in.
-
Data Quality Issues: Cleanse outdated data before migrating to the new system.
-
High Initial Costs: Initiate a pilot program to demonstrate potential ROI before full implementation.
The Future of SCMCompile and Supply Chain Technology
Experts predict that the future will see further integration of technologies like AI, IoT, and blockchain reshaping SCM. Upcoming trends include:
-
Autonomous Logistics: Think self-driving trucks and drone deliveries.
-
Hyper-Personalized Supply Chains: Custom packaging and swift last-mile delivery solutions.
-
Sustainability Analytics: Monitoring carbon footprints and promoting eco-friendly practices.
Final Thoughts: Is SCMCompile Right for Your Business?
If your organization struggles with issues such as:
-
Excess inventory costs
-
Late shipments
-
Supplier reliability challenges
Then SCMCompile could be a transformative solution for your supply chain management. Start with a trial, assess the improvements, and gradually scale the implementation.
Pro Tip: Pair SCMCompile with a robust change management strategy to maximize adoption and achieve standout results.
Technology
A Guide to Planning a Multilingual Online Event
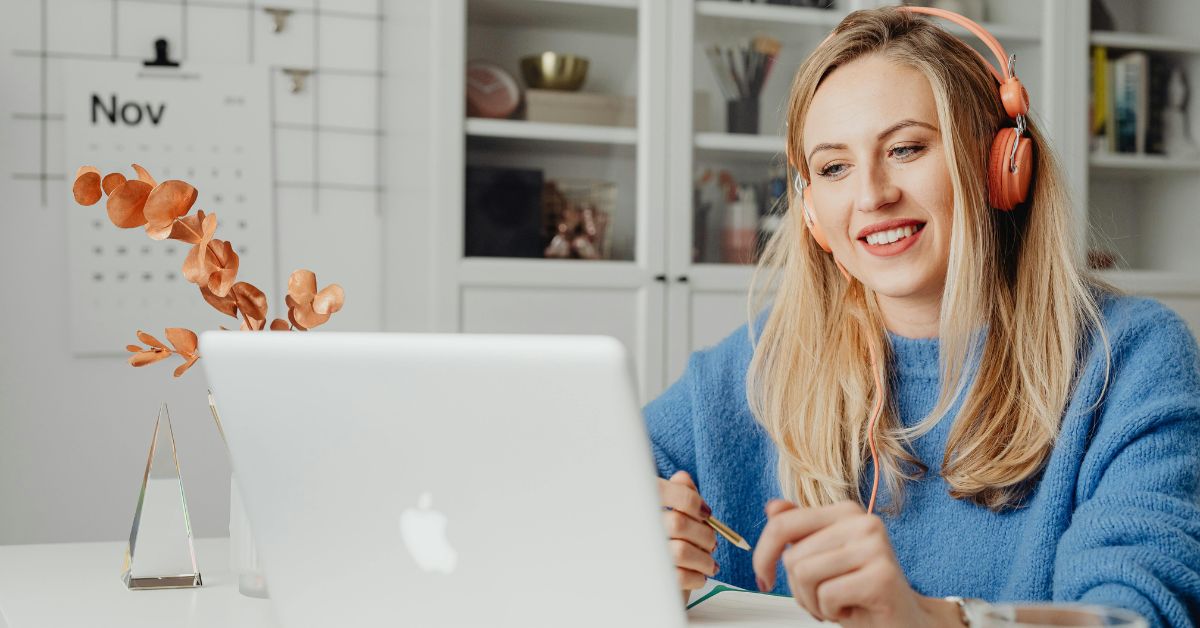
When people connect from different parts of the world, it’s only natural that they don’t all speak the same language. Still, it’s increasingly common for them to share the same screen. The rise of global meetings, digital conferences, product launches, and hybrid events is removing physical barriers—but it’s also challenging us to rethink how we communicate. A stable internet connection and a user-friendly platform are no longer enough. Effective communication in remote events now requires considering what each participant hears, sees, and understands—regardless of the language they think in.
Why Language Decisions Should Be Made Early
One of the most common mistakes in planning virtual events is leaving the language component until the end. In reality, language should be considered from the very first draft of the event. This doesn’t just mean deciding whether to include subtitles, live interpretation, or voiceover—it means understanding the expectations of your audience, their roles, and how they’ll interact.
One thing truly global events have in common is that they view their audience as a diverse group with varying levels of language fluency—and they actively work to include everyone in the experience. This is achieved by combining a variety of tools and services that make up the current landscape of language solutions. There’s no one-size-fits-all approach. It’s about identifying the best format for each type of content, determining what’s technically feasible, and ensuring a consistent, high-quality experience for all participants.
When to Use Subtitles, Interpretation, or Voiceover
Not every strategy works for every event. The key is selecting the right tool for the type of communication you’re delivering. For events with single speakers and linear presentations, simultaneous interpretation is often the best choice. It allows each attendee to choose their preferred audio channel and listen in real time in their own language. However, this setup requires reliable technical infrastructure, professional interpreters, and pre-event coordination with speakers.
For more visual events—or ones where accuracy is critical, such as technical product launches or training sessions—real-time subtitles might be a better fit. They support viewers who partially understand the original language and enhance accessibility for people with hearing impairments. In these cases, fast, clear, and accurate transcription is essential.
Voiceover, though less common for live events, can be valuable for pre-recorded webinars or content that will be shared post-event. Its main advantage is delivering a fully localized experience, though it requires more time and editing. Some companies even combine formats—offering live interpretation during the event and a dubbed version for on-demand distribution later.
The Limits of Machine Translation for Live Events
AI-powered tools have greatly expanded the availability of automatic translation and subtitling. While they can be helpful in informal settings, they still have major limitations when it comes to quality, nuance, and context. In most professional or corporate settings, automated translation should be used with caution.
Human input is still crucial for ensuring accuracy and adapting tone, cultural references, and expressions. A trained interpreter can convey intent and emotion in ways that algorithms simply can’t—at least not yet. So while technology can assist, suggest, or accelerate certain tasks, it does not replace the need for thoughtful planning and expert curation in serious multilingual events.
Technical implementation also requires attention. Choosing a streaming or video conferencing platform that supports multiple audio tracks, interpretation channels, or synchronized subtitles is not a trivial decision. Specialized tools exist for this, and testing them well in advance is highly recommended.
Preparing the Tech Team and Interpreters
Beyond technology, events are still a human experience. That means the team involved needs to be properly prepared. If your event includes live interpreters, it’s essential to provide them with all presentation materials in advance, clearly define their shifts, and ensure they have an appropriate acoustic and technical setup. The same goes for moderators and presenters: they must know how to activate multilingual features, guide the audience, and answer common participant questions.
In large events or ones with multiple simultaneous sessions, it can be helpful to assign a dedicated language coordination manager. This person ensures that each language channel is running smoothly and can assist attendees facing technical issues. Their role becomes even more valuable when the audience includes participants with limited digital literacy or accessibility challenges.
Multilingual Virtual Event Planning Checklist
Planning a multilingual online event can be complex—but much easier when you follow a clear roadmap. This checklist offers a foundational guide to help you deliver a smooth, professional experience:
Before the event:
- Define the primary languages and delivery methods (audio, subtitles, voiceover)
- Choose experienced providers for interpretation, subtitling, or dubbing
- Confirm that your platform supports multiple audio tracks and/or subtitles
- Train the technical team and moderators on multilingual features
- Run a full event rehearsal including interpretation or subtitling
- Send interpreters all relevant materials: presentations, glossaries, agenda
During the event:
- Activate and test language channels before going live
- Guide attendees on how to access their preferred language
- Set up a tech support channel to handle attendee questions
- Monitor audio quality across all channels
- Coordinate interpreter transitions for long sessions
After the event:
- Evaluate the quality of interpretation or subtitles
- Collect feedback from attendees on their language experience
- Use feedback to improve future events
- Prepare edited versions with dubbing or subtitles for post-event sharing
- Publicly thank your language and technical teams
Beyond Language, It’s About What You Share
Thinking in multiple languages isn’t just a nice-to-have—it’s a way to design more inclusive events where ideas aren’t lost in translation but flow freely. The strength of a global audience lies in its diversity, and each language is a doorway into that shared conversation. Planning with this in mind can be the difference between a meeting that’s simply heard—and one that’s truly understood.
Technology
The Scale Blank: How to choose Perfect One for Your Needs
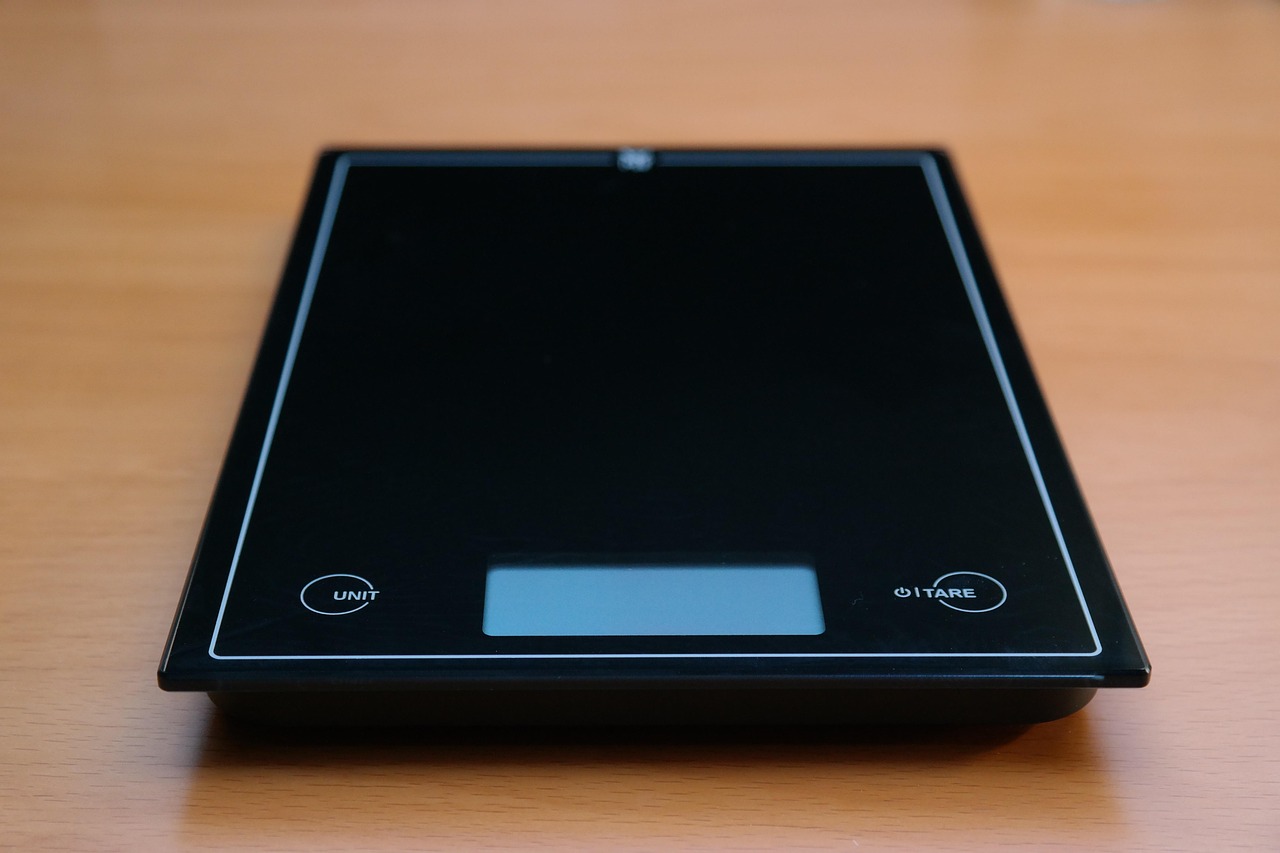
Have you ever wondered why some kitchen scales perform flawlessly while others fail within months? The secret often lies in an overlooked component—the scale blank. Whether you’re a home cook, a professional chef, or a business owner, choosing the right scale blank can make all the difference in accuracy, durability, and performance.
In this guide, we’ll break down everything you need to know about scale blanks—what they are, why they matter, and how to pick the best one for your needs.
What Is a Scale Blank?
A scale blank is the foundational platform of a weighing scale where items are placed for measurement. It’s the flat surface (usually made of stainless steel, glass, or plastic) that interacts directly with whatever you’re weighing.
Why Does It Matter?
-
Accuracy: A poorly designed blank can flex or warp, leading to incorrect readings.
-
Durability: The material determines how well it resists scratches, stains, and wear.
-
Hygiene: Some blanks are easier to clean, making them ideal for food or medical use.
Types of Scale Blanks: Pros and Cons
Not all scale blanks are created equal. Here’s a breakdown of the most common types:
1. Stainless Steel Blanks
✅ Pros:
-
Highly durable and resistant to corrosion
-
Easy to clean (ideal for kitchens and labs)
-
Provides a stable weighing surface
❌ Cons:
-
Can be slippery for lightweight items
-
Prone to fingerprints and smudges
Best for: Commercial kitchens, laboratories, and industrial settings.
2. Glass Blanks
✅ Pros:
-
Sleek, modern appearance
-
Easy to wipe clean
-
Doesn’t absorb odors or stains
❌ Cons:
-
Fragile—can crack under heavy weight
-
Slippery for certain items
Best for: Home kitchens, bakeries, and retail displays.
3. Plastic Blanks
✅ Pros:
-
Lightweight and affordable
-
Resistant to minor impacts
-
Non-slip surface in some models
❌ Cons:
-
Less durable over time
-
Can absorb stains and odors
Best for: Budget-friendly home scales or portable options.
How to Choose the Right Scale Blank
Picking the best scale blank depends on your specific needs. Here’s what to consider:
1. Intended Use
-
Cooking/Baking? Stainless steel or glass for easy cleaning.
-
Industrial Weighing? Reinforced stainless steel for durability.
-
Portable Scale? Lightweight plastic for convenience.
2. Weight Capacity
-
Small kitchen scales (1–10 lbs): Glass or plastic.
-
Heavy-duty scales (50+ lbs): Thick stainless steel.
3. Maintenance & Cleaning
-
Stainless steel: Wipe with a damp cloth.
-
Glass: Use glass cleaner for shine.
-
Plastic: Avoid abrasive cleaners to prevent scratches.
4. Anti-Slip Features
Some blanks have textured surfaces or rubberized edges to prevent items from sliding off.
5. Budget
-
Premium: Stainless steel
-
Mid-range: Tempered glass
-
Budget-friendly: High-quality plastic
Real-World Examples: Where Scale Blanks Make a Difference
Example 1: Bakery Business
A bakery switched from plastic to stainless steel blanks and saw fewer inaccuracies in dough measurements, leading to more consistent products.
Example 2: Home Cooks
A home chef using a glass scale blank found it easier to clean after measuring sticky ingredients like honey or syrup.
Example 3: Lab Environments
A research lab using high-grade stainless steel blanks avoided corrosion from chemical spills, ensuring long-term reliability.
Expert Tips for Maintaining Your Scale Blank
To extend the lifespan of your scale blank:
✔ Clean regularly—avoid buildup of debris.
✔ Avoid overloading—stick to the maximum weight limit.
✔ Store properly—keep in a dry place to prevent rust (for metal blanks).
✔ Check for damage—cracks or warping can affect accuracy.
Final Thoughts: Why Your Scale Blank Choice Matters
The scale blank might seem like a small detail, but it plays a crucial role in the accuracy and longevity of your weighing scale. Whether you’re a home cook, a business owner, or a lab technician, choosing the right material and maintaining it properly ensures reliable measurements every time.
Ready to upgrade your scale? Now that you know what to look for, you can make an informed decision and get the best performance out of your weighing device.
FAQs About Scale Blanks
Can I replace a damaged scale blank?
Yes, many manufacturers sell replacement blanks. Check compatibility before purchasing.
Are there antimicrobial scale blanks?
Some stainless steel blanks have antimicrobial coatings, ideal for medical or food industries.
How do I know if my scale blank is affecting accuracy?
If your scale gives inconsistent readings, inspect the blank for warping or damage.
-
Articles5 months ago
How Many Times Can You Regrow Green Onions
-
Fashion10 months ago
Opals in the USA: A Gemstone Transforming the Crystal Healing Market
-
News1 year ago
Understanding HotLeaks: What You Need to Know
-
Entertainment9 months ago
How to Use Snaptik: A Complete Guide to Download TikTok Videos
-
Technology1 year ago
The Wonders of Oh Em Gee Blog
-
Entertainment1 year ago
Bare it All: Unforgettable Skinny Dipping Stories Shared
-
Health1 year ago
Can You Smoke Shrooms? Exploring the Myths and Realities
-
Busniess5 months ago
Why Is Business Part of Science: Strategy, Innovation Explained