Technology
Injection Mold Design for High-Volume Production: Best Practices for Durability and Efficiency
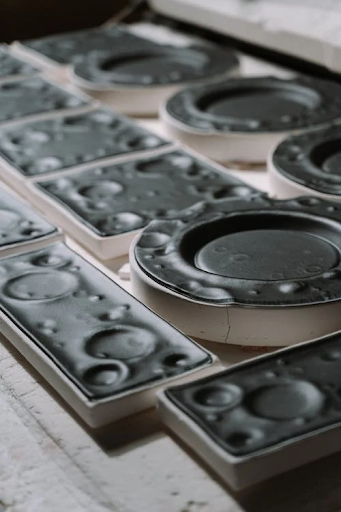
Injection molding is a vital technique that increases cost efficiency, speed, and product quality. It offers a reliable solution for manufacturers looking to mass-produce their products. It also comes with massive benefits like reducing time to market and costs. Durability and cost efficiency are critical for manufacturers. Creating quality products at reasonable prices while spending less time on every dispatch keeps your clients happy. Mass production of plastic parts is possible with injection mold design. Here’s an outlook on injection mold design for high-volume production and the best practices for durability and efficiency.
Understanding Injection Molding and Its Challenges
The injection molding process makes it possible to produce identical plastic parts cost-effectively and efficiently. The process starts with quickly injecting molten plastic into a molding cavity. The plastic cools and solidifies forming desired shapes. The process is automated to ensure rapid production and that the parts created are identical. Large productions range from a thousand to 1 million parts produced annually. Manufacturers face several challenges during production like wear and tear, cycle time, and accuracy. Producing large batches of parts requires more time and resources. You want solutions that cut costs and minimize losses due to product deficits in every batch. Injection mold design ensures uniformity of product and maintains quality.
Designing for Durability: Key Consideration
Durability entails the ability to withstand conditions of operation without needing maintenance. Different plastic materials have varying degrees of flexibility, strength, durability, and heat resistance. When picking the right material, you determine the quality of the finished product. Strong resin materials like Acrylonitrile Butadiene Styrene ABS, handle heat well and are suitable for creating automotive parts, household items, and acrylics.
Mold maintenance is yet another factor to consider. You should have a plan for mold maintenance. Good maintenance practices keep molds in great shape reducing inconsistencies during production. Your cooling channels should be in the right place to reduce warping. Cooling channels and surface finishes need care and maintenance. Regular maintenance ensures your production plant lasts long and gives you quality output. Good mold design ensures an optimized resin flow for uniformity. It also ensures zero overflows to protect the surfaces.
The mold designs you choose should optimize your product and enhance durability. Mold designs should be practical. You should utilize designers who understand the intricacies of manufacturing. Experienced designers utilize computer-aided designs that suit your production needs. The designs go beyond the shapes and sizes of the product to incorporate other needs like uniformity.
Maximizing Efficiency in High-Volume Production
You can maximize efficiency in a high-volume production. Certain aspects like the cooling channel design determine the output. You also regulate cooling, venting, and gating processes during production. The cooling time and the cooling temperature also impact the finished product. When automating and optimizing the processes, ensure that you give ample time to a part spent inside a mold before ejection. To optimize cycle time, you should ensure that the designs have uniform wall thickness and avoid complex geometries. Ultimately, these will reduce the cooling time.
Automation and robotics are your allies in mass production. Manufacturing experts create systems that ensure the manufacturing processes are smooth and effective. Every little process is automated to enhance efficiency. Automation also helps reduce wastage and cuts cycle time. Robotics, on the other hand, ensures that you get beyond human capabilities to handle manual tasks during production. Robotics arms remove the products from the molds once they cool off. They can also load plastic pallets into the injection molding machine.
Production defects waste your time and money. You should invest in precise mold designs to reduce the risk of defects during the manufacturing process. You can outsource mold designing to professionals at China Injection Mold. They have everything you need to build the right injection molds. Good designs work well with your choice of resin material to give a quality product.
Best Practices for Cost Control and Long-Term Performance
You may feel overwhelmed with initial mold design costs and the investment it takes to start your plastic manufacturing business. While cheap resins are easy and more affordable to manufacture, they compromise product quality. Your customers will not enjoy the products. Initial investments may mean long-term gains when used strategically. Quality mold designs reduce cycle time, cut waste, and serve you longer. They also cut maintenance costs.
Proper design is crucial to optimizing the whole production process. While you will spend money on proper designs, they set the pace for your business. Problems like machine breakdown, low-quality output, and product defects will force you to dig deeper into your pocket. Proper molds produce durable products that your customers will swear by, making your venture profitable. The proper design molds save energy and increase output. High-volume injection molding increases production while maintaining quality.
Put in place improvement strategies for improving mold performance over time. Cleaning molds can help them last longer. Immersing molds in a strong solvent can help repair the damage over time reducing wear and tear. Lubricating mold components also enhances mold performance. Schedule quality control checks to ensure your molds are working well. The checks should include testing that the molds are in great shape. Regular inspection and repairs ensure that no breakdown catches you off guard and interrupts the production process. Lastly, replace broken and damaged molds regularly. When molds break down beyond repair, get replacements to avoid compromising the product. That will save you the headache of batch recalls.
Conclusion
No doubt mold designs are the heart of plastic manufacturing processes. You should ensure your injection molds are efficient and outstanding. Injection molds should be durable. The designs should have the right wall thickness and use suitable material to support the process. The injection molds should also utilize simple geometric angles to ease the manufacturing process.
Effective mold design can drive high-volume production success. The best mold designs are efficient. They also have high turnover rates of quality products increasing production. Investing in effective mold designs increases your company’s profitability, reduces production stress, and fosters great customer relations.
Technology
A Guide to Planning a Multilingual Online Event
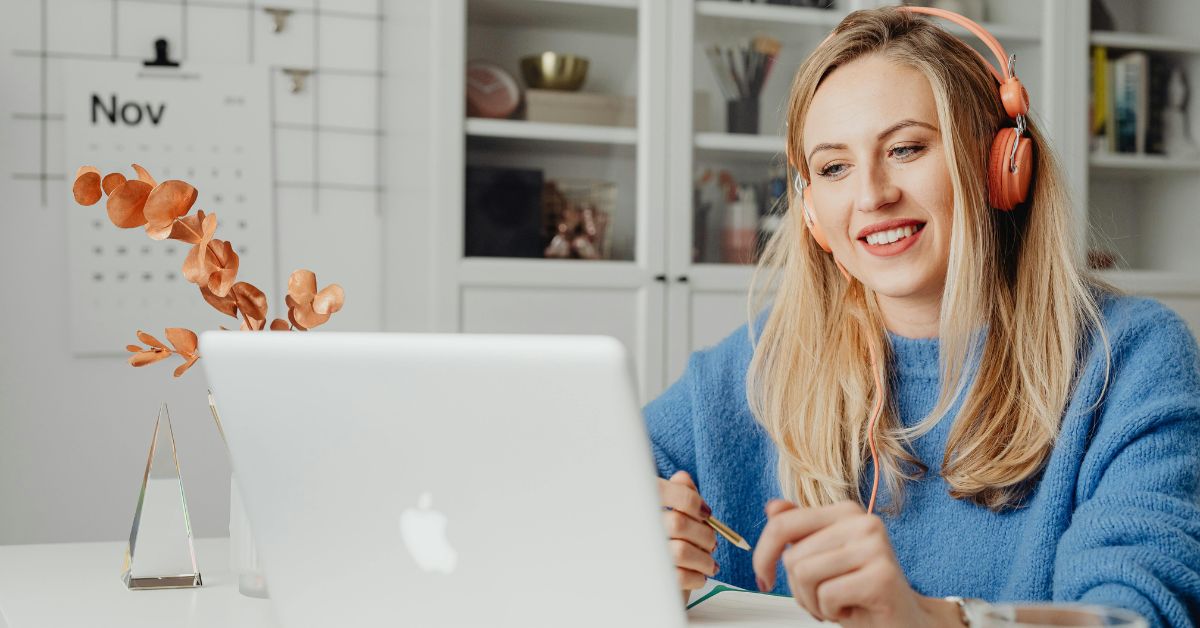
When people connect from different parts of the world, it’s only natural that they don’t all speak the same language. Still, it’s increasingly common for them to share the same screen. The rise of global meetings, digital conferences, product launches, and hybrid events is removing physical barriers—but it’s also challenging us to rethink how we communicate. A stable internet connection and a user-friendly platform are no longer enough. Effective communication in remote events now requires considering what each participant hears, sees, and understands—regardless of the language they think in.
Why Language Decisions Should Be Made Early
One of the most common mistakes in planning virtual events is leaving the language component until the end. In reality, language should be considered from the very first draft of the event. This doesn’t just mean deciding whether to include subtitles, live interpretation, or voiceover—it means understanding the expectations of your audience, their roles, and how they’ll interact.
One thing truly global events have in common is that they view their audience as a diverse group with varying levels of language fluency—and they actively work to include everyone in the experience. This is achieved by combining a variety of tools and services that make up the current landscape of language solutions. There’s no one-size-fits-all approach. It’s about identifying the best format for each type of content, determining what’s technically feasible, and ensuring a consistent, high-quality experience for all participants.
When to Use Subtitles, Interpretation, or Voiceover
Not every strategy works for every event. The key is selecting the right tool for the type of communication you’re delivering. For events with single speakers and linear presentations, simultaneous interpretation is often the best choice. It allows each attendee to choose their preferred audio channel and listen in real time in their own language. However, this setup requires reliable technical infrastructure, professional interpreters, and pre-event coordination with speakers.
For more visual events—or ones where accuracy is critical, such as technical product launches or training sessions—real-time subtitles might be a better fit. They support viewers who partially understand the original language and enhance accessibility for people with hearing impairments. In these cases, fast, clear, and accurate transcription is essential.
Voiceover, though less common for live events, can be valuable for pre-recorded webinars or content that will be shared post-event. Its main advantage is delivering a fully localized experience, though it requires more time and editing. Some companies even combine formats—offering live interpretation during the event and a dubbed version for on-demand distribution later.
The Limits of Machine Translation for Live Events
AI-powered tools have greatly expanded the availability of automatic translation and subtitling. While they can be helpful in informal settings, they still have major limitations when it comes to quality, nuance, and context. In most professional or corporate settings, automated translation should be used with caution.
Human input is still crucial for ensuring accuracy and adapting tone, cultural references, and expressions. A trained interpreter can convey intent and emotion in ways that algorithms simply can’t—at least not yet. So while technology can assist, suggest, or accelerate certain tasks, it does not replace the need for thoughtful planning and expert curation in serious multilingual events.
Technical implementation also requires attention. Choosing a streaming or video conferencing platform that supports multiple audio tracks, interpretation channels, or synchronized subtitles is not a trivial decision. Specialized tools exist for this, and testing them well in advance is highly recommended.
Preparing the Tech Team and Interpreters
Beyond technology, events are still a human experience. That means the team involved needs to be properly prepared. If your event includes live interpreters, it’s essential to provide them with all presentation materials in advance, clearly define their shifts, and ensure they have an appropriate acoustic and technical setup. The same goes for moderators and presenters: they must know how to activate multilingual features, guide the audience, and answer common participant questions.
In large events or ones with multiple simultaneous sessions, it can be helpful to assign a dedicated language coordination manager. This person ensures that each language channel is running smoothly and can assist attendees facing technical issues. Their role becomes even more valuable when the audience includes participants with limited digital literacy or accessibility challenges.
Multilingual Virtual Event Planning Checklist
Planning a multilingual online event can be complex—but much easier when you follow a clear roadmap. This checklist offers a foundational guide to help you deliver a smooth, professional experience:
Before the event:
- Define the primary languages and delivery methods (audio, subtitles, voiceover)
- Choose experienced providers for interpretation, subtitling, or dubbing
- Confirm that your platform supports multiple audio tracks and/or subtitles
- Train the technical team and moderators on multilingual features
- Run a full event rehearsal including interpretation or subtitling
- Send interpreters all relevant materials: presentations, glossaries, agenda
During the event:
- Activate and test language channels before going live
- Guide attendees on how to access their preferred language
- Set up a tech support channel to handle attendee questions
- Monitor audio quality across all channels
- Coordinate interpreter transitions for long sessions
After the event:
- Evaluate the quality of interpretation or subtitles
- Collect feedback from attendees on their language experience
- Use feedback to improve future events
- Prepare edited versions with dubbing or subtitles for post-event sharing
- Publicly thank your language and technical teams
Beyond Language, It’s About What You Share
Thinking in multiple languages isn’t just a nice-to-have—it’s a way to design more inclusive events where ideas aren’t lost in translation but flow freely. The strength of a global audience lies in its diversity, and each language is a doorway into that shared conversation. Planning with this in mind can be the difference between a meeting that’s simply heard—and one that’s truly understood.
Technology
The Scale Blank: How to choose Perfect One for Your Needs
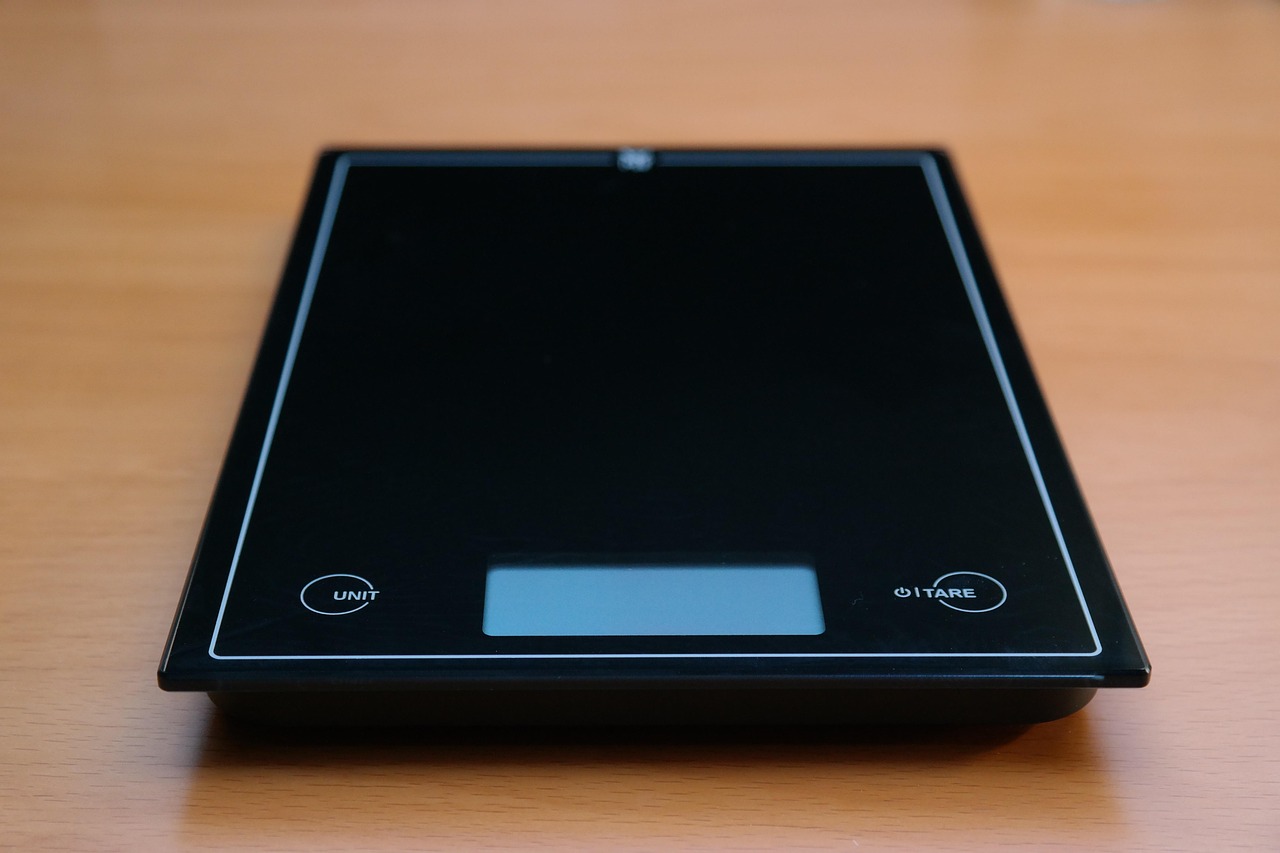
Have you ever wondered why some kitchen scales perform flawlessly while others fail within months? The secret often lies in an overlooked component—the scale blank. Whether you’re a home cook, a professional chef, or a business owner, choosing the right scale blank can make all the difference in accuracy, durability, and performance.
In this guide, we’ll break down everything you need to know about scale blanks—what they are, why they matter, and how to pick the best one for your needs.
What Is a Scale Blank?
A scale blank is the foundational platform of a weighing scale where items are placed for measurement. It’s the flat surface (usually made of stainless steel, glass, or plastic) that interacts directly with whatever you’re weighing.
Why Does It Matter?
-
Accuracy: A poorly designed blank can flex or warp, leading to incorrect readings.
-
Durability: The material determines how well it resists scratches, stains, and wear.
-
Hygiene: Some blanks are easier to clean, making them ideal for food or medical use.
Types of Scale Blanks: Pros and Cons
Not all scale blanks are created equal. Here’s a breakdown of the most common types:
1. Stainless Steel Blanks
✅ Pros:
-
Highly durable and resistant to corrosion
-
Easy to clean (ideal for kitchens and labs)
-
Provides a stable weighing surface
❌ Cons:
-
Can be slippery for lightweight items
-
Prone to fingerprints and smudges
Best for: Commercial kitchens, laboratories, and industrial settings.
2. Glass Blanks
✅ Pros:
-
Sleek, modern appearance
-
Easy to wipe clean
-
Doesn’t absorb odors or stains
❌ Cons:
-
Fragile—can crack under heavy weight
-
Slippery for certain items
Best for: Home kitchens, bakeries, and retail displays.
3. Plastic Blanks
✅ Pros:
-
Lightweight and affordable
-
Resistant to minor impacts
-
Non-slip surface in some models
❌ Cons:
-
Less durable over time
-
Can absorb stains and odors
Best for: Budget-friendly home scales or portable options.
How to Choose the Right Scale Blank
Picking the best scale blank depends on your specific needs. Here’s what to consider:
1. Intended Use
-
Cooking/Baking? Stainless steel or glass for easy cleaning.
-
Industrial Weighing? Reinforced stainless steel for durability.
-
Portable Scale? Lightweight plastic for convenience.
2. Weight Capacity
-
Small kitchen scales (1–10 lbs): Glass or plastic.
-
Heavy-duty scales (50+ lbs): Thick stainless steel.
3. Maintenance & Cleaning
-
Stainless steel: Wipe with a damp cloth.
-
Glass: Use glass cleaner for shine.
-
Plastic: Avoid abrasive cleaners to prevent scratches.
4. Anti-Slip Features
Some blanks have textured surfaces or rubberized edges to prevent items from sliding off.
5. Budget
-
Premium: Stainless steel
-
Mid-range: Tempered glass
-
Budget-friendly: High-quality plastic
Real-World Examples: Where Scale Blanks Make a Difference
Example 1: Bakery Business
A bakery switched from plastic to stainless steel blanks and saw fewer inaccuracies in dough measurements, leading to more consistent products.
Example 2: Home Cooks
A home chef using a glass scale blank found it easier to clean after measuring sticky ingredients like honey or syrup.
Example 3: Lab Environments
A research lab using high-grade stainless steel blanks avoided corrosion from chemical spills, ensuring long-term reliability.
Expert Tips for Maintaining Your Scale Blank
To extend the lifespan of your scale blank:
✔ Clean regularly—avoid buildup of debris.
✔ Avoid overloading—stick to the maximum weight limit.
✔ Store properly—keep in a dry place to prevent rust (for metal blanks).
✔ Check for damage—cracks or warping can affect accuracy.
Final Thoughts: Why Your Scale Blank Choice Matters
The scale blank might seem like a small detail, but it plays a crucial role in the accuracy and longevity of your weighing scale. Whether you’re a home cook, a business owner, or a lab technician, choosing the right material and maintaining it properly ensures reliable measurements every time.
Ready to upgrade your scale? Now that you know what to look for, you can make an informed decision and get the best performance out of your weighing device.
FAQs About Scale Blanks
Can I replace a damaged scale blank?
Yes, many manufacturers sell replacement blanks. Check compatibility before purchasing.
Are there antimicrobial scale blanks?
Some stainless steel blanks have antimicrobial coatings, ideal for medical or food industries.
How do I know if my scale blank is affecting accuracy?
If your scale gives inconsistent readings, inspect the blank for warping or damage.
Technology
Why You Need to Check Out the Socks5 Proxy List Wingate.me
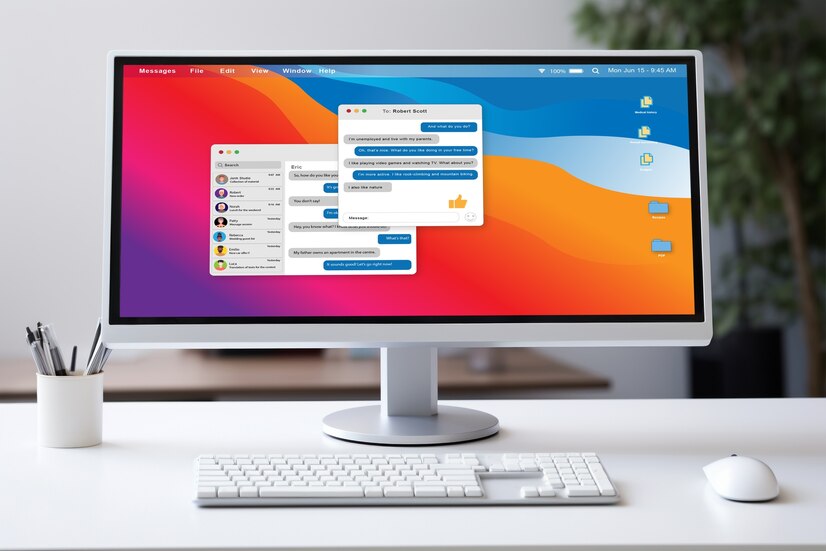
Looking to enhance your online security and privacy? Dive into the world of private proxies with Wingate.me’s Socks5 Proxy List! Whether you’re a seasoned web user or just starting out, this comprehensive list offers unparalleled protection and browsing freedom. Let’s explore why checking out Wingate.me’s Socks5 Proxy List is a game-changer for your online experience.
Navigation Menu
When it comes to navigating Wingate.me’s Socks5 Proxy List, the user-friendly interface makes finding what you need a breeze. The navigation menu is thoughtfully designed for easy access to various features and options, ensuring a seamless browsing experience. With clear labels and intuitive organization, you can quickly locate specific tools or settings without any hassle.
The menu layout allows users to navigate effortlessly between different sections of the proxy list, making it simple to switch between saved searches, repository files, latest commits, and more. Whether you’re a beginner or an advanced user, the navigation menu caters to all levels of expertise with its straightforward design and functionality.
By utilizing the navigation menu effectively, users can maximize their productivity and efficiency when exploring Wingate.me’s Socks5 Proxy List. Take advantage of this well-structured tool to streamline your browsing experience and unlock the full potential of private proxies for enhanced online security and privacy.
Use Saved Searches to Filter Your Results More Quickly
When browsing through a socks5 proxy list on Wingate.me, efficiency is key. One handy feature to streamline your search process is utilizing saved searches to filter results quickly. By saving specific search criteria such as location, speed, or anonymity level, you can access relevant proxies in just a few clicks.
This time-saving tool ensures that you don’t have to input the same filters repeatedly every time you revisit the site. Simply set your preferences once and let Wingate.me do the rest. Whether you’re looking for proxies for data scraping, geo-blocked content access, or cybersecurity purposes, using saved searches can help tailor your results to meet your exact needs.
With this functionality at your disposal, finding the perfect socks5 proxy becomes a breeze. Say goodbye to sifting through irrelevant options – optimize your search experience with saved searches on Wingate.me today!
Folders and Files
When it comes to navigating through the Socks5 Proxy List on Wingate.me, understanding the organization of folders and files is key. Each folder contains a specific category of proxies, neatly arranged for easy access. From streaming proxies to gaming proxies, you can find them all conveniently sorted within their respective folders.
Files within each folder provide detailed information about each proxy, including its speed, location, and anonymity level. This allows users to make informed decisions when selecting the right proxy for their needs. Whether you’re looking for fast speeds or reliable connections, exploring the various files in each folder can help you find the perfect match.
By utilizing the intuitive folder and file structure on Wingate.me’s Socks5 Proxy List, users can efficiently browse through different categories and options available to them. Easy navigation means less time searching and more time enjoying seamless proxy connections for all your online activities.
Latest Commit
Are you someone who always wants to stay up-to-date with the latest changes in your favorite projects? Well, at Wingate.me, we understand the importance of keeping track of the “Latest Commit” on our Socks5 Proxy List repository.
The “Latest Commit” feature allows you to see the most recent updates made to our proxy list, giving you real-time insights into any new additions or modifications. Whether it’s bug fixes, performance enhancements, or exciting new features, staying informed about the latest commit can help you make informed decisions when choosing proxies for your online activities.
By regularly checking out the latest commit section on Wingate.me’s platform, you can ensure that you are always using the most updated and optimized version of our socks5 proxy list. Stay ahead of the game and maximize your browsing experience by staying connected to our repository’s latest developments!
History
Have you ever wondered about the history of a website or online platform? The “History” section on Wingate.me provides valuable insights into past activities and changes made to the Socks5 proxy list. It’s like taking a trip down memory lane, seeing how the service has evolved over time.
By exploring this feature, users can track updates, modifications, and improvements implemented by Wingate.me. This historical perspective allows for a better understanding of how the platform has developed and adapted to meet user needs effectively.
Delving into the History section offers transparency and accountability as users can trace back any alterations or additions that have been made. It adds a layer of trust and reliability to the overall service provided by Wingate.me.
Repository Files Navigation
When it comes to navigating through repository files on Wingate.me, efficiency is key. The platform offers a seamless experience for users to locate and access specific files within their repositories effortlessly.
With intuitive search functionalities and organized file structures, finding the exact document you need becomes a breeze. Whether you’re looking for code snippets, configuration files, or any other data stored in your repository, Wingate.me streamlines the process.
By providing clear pathways to navigate through folders and subfolders, users can quickly drill down to the desired file without wasting time on unnecessary clicks. This user-friendly approach enhances productivity and ensures that developers can focus on their tasks rather than getting lost in complex directory structures.
Wingate.me’s repository files navigation feature simplifies file management and facilitates smooth collaboration among team members working on shared projects.
Releases
When it comes to the “Releases” section on Wingate.me’s Socks5 Proxy List, users can stay updated on the latest changes and improvements. This feature allows for easy tracking of when new versions or updates are launched, ensuring that you have access to the most current resources available.
By regularly checking the “Releases” tab, you can see any bug fixes, enhancements, or additional features that have been implemented into the proxy list. This transparency enables users to understand what modifications have been made and how they may impact their browsing experience.
Whether it’s a minor tweak or a significant upgrade, staying informed through the “Releases” section ensures that you are always aware of any advancements in Wingate.me’s Socks5 Proxy List. Stay ahead by keeping an eye on this section for any new developments that could benefit your proxy usage.
Packages
When it comes to exploring the functionalities and utilities of Wingate.me, the “Packages” feature stands out as a valuable tool for users. This section provides access to various pre-packaged sets of resources, tools, or configurations that can streamline your workflow and enhance your browsing experience.
By accessing packages through Wingate.me, users can easily integrate additional features or enhancements into their proxy setup without the hassle of manual configuration. Whether you’re looking for security add-ons, performance optimizations, or specialized tools, the Packages section offers a curated selection to choose from.
Each package is designed to cater to specific needs and preferences, allowing users to customize their proxy settings according to their requirements. From enhancing privacy protocols to optimizing connection speeds, these packages offer a convenient way to enhance your online activities effortlessly.
Exploring the Packages section on Wingate.me opens up a world of possibilities for maximizing the efficiency and effectiveness of your proxy usage. Unlock new capabilities and functionalities with just a few clicks in this dynamic repository of resources tailored for discerning users like yourself.
Footer
The footer section on a website might seem small, but it plays a significant role in user experience. It’s the final impression visitors have before leaving your site. The footer is like the cherry on top of a sundae – a finishing touch that ties everything together.
In the footer, you can find important links like contact information, privacy policies, terms and conditions, and social media icons for easy navigation. These elements help users feel more comfortable exploring your site and potentially converting into customers.
Design-wise, the footer can also showcase your brand’s personality through color schemes, fonts, and creative layouts. A well-designed footer not only looks professional but also enhances the overall aesthetics of your website.
Don’t underestimate the power of a well-crafted footer – it may be at the bottom of the page, but its impact on user engagement and satisfaction is anything but minor.
What Is A Socks5 Proxy?
Have you ever wondered how to enhance your online privacy and security while browsing the internet? Well, a Socks5 proxy might just be the solution you’re looking for.
In simple terms, a Socks5 proxy acts as an intermediary server between your device and the internet. When you connect to the internet through a Socks5 proxy, your IP address is masked, making it harder for websites to track your online activities.
Unlike traditional proxies, Socks5 proxies are highly versatile and can handle various types of traffic such as HTTP, HTTPS, FTP, and more. This flexibility makes them ideal for tasks like torrenting or accessing geo-restricted content.
Additionally, Socks5 proxies offer faster speeds and better performance compared to other proxy options. With its advanced features and benefits, using a Socks5 proxy can significantly improve your online experience by providing an extra layer of anonymity and security.
What Is Private Proxy Wingate.me?
Private Proxy Wingate.me offers a secure way to browse the internet anonymously. With this service, users can mask their IP addresses, enhancing privacy and security online. By utilizing private proxies, individuals can access websites without revealing their true location or identity.
Wingate.me’s private proxy service allows for seamless browsing without restrictions. Whether you’re accessing geo-blocked content or simply prioritizing your privacy, these proxies provide a reliable solution. Through encrypted connections, Wingate.me ensures that your data remains protected while surfing the web.
With Private Proxy Wingate.me, users can enjoy faster connection speeds and reduced latency compared to public proxies. This advantage is especially beneficial for activities like streaming or online gaming where performance matters. Additionally, Wingate.me offers dedicated customer support to assist with any technical issues that may arise when using their private proxy services.
In today’s digital landscape where privacy is paramount, Private Proxy Wingate.me stands out as a trusted provider of secure internet browsing solutions.
Types of Private Proxy Wingate.me
When it comes to private proxies, Wingate.me offers a variety of options to suit different needs and preferences.
One type of private proxy available on Wingate.me is the dedicated proxy. This type allocates a single IP address exclusively for your use, providing enhanced security and reliability for your online activities.
Another option is the rotating proxy offered by Wingate.me. With this type, you can automatically switch between multiple IP addresses at set intervals, allowing you to access diverse geo-locations and avoid detection.
Moreover, Wingate.me also provides shared proxies which are cost-effective solutions for those looking to mask their online identity without breaking the bank.
Each type of private proxy from Wingate.me caters to specific requirements, whether it’s individualized security measures or budget-friendly anonymity.
An Overview Of Wingate.me’s Socks5 Proxy List
At Wingate.me, the Socks5 proxy list is a powerful tool for enhancing your online security and privacy. This list provides users with access to a vast array of high-speed proxies that can help mask their IP addresses and encrypt their internet traffic. With the Socks5 protocol, you can enjoy fast and reliable connections while keeping your browsing activities anonymous.
The Socks5 proxy list offered by Wingate.me is regularly updated to ensure that users have access to the latest and most secure proxies available. Whether you’re looking to bypass geo-restrictions, protect your personal information from prying eyes, or simply enhance your online anonymity, this proxy list has got you covered.
By utilizing Wingate.me’s Socks5 proxy list, you can take control of your online experience and browse the web with confidence. Stay safe and secure while enjoying unrestricted access to content from around the globe.
The Benefits of Wingate.me’s Socks5 Proxy List
When it comes to online security and anonymity, Wingate.me’s Socks5 Proxy List offers a range of benefits that users can take advantage of. One key benefit is the enhanced level of privacy it provides by masking your IP address, making it harder for third parties to track your online activities.
Another advantage is the ability to bypass geo-restrictions and access content that may be blocked in your region. This can be particularly useful for streaming services or websites with regional restrictions.
Moreover, Wingate.me’s Socks5 Proxy List offers faster connection speeds compared to other proxy types, ensuring smooth browsing and minimal lag while maintaining a secure connection. This can be crucial for tasks that require high bandwidth or real-time data transfer.
Additionally, using Wingate.me’s Socks5 Proxy List adds an extra layer of security when connecting to public Wi-Fi networks, protecting your sensitive information from potential threats such as hackers or malicious software.
How To Set Up Wingate.me’s Socks5 Proxy?
Setting up Wingate.me’s Socks5 proxy is a straightforward process that allows you to enhance your online privacy and security. To begin, you first need to visit the Wingate.me website and sign up for an account. Once registered, navigate to the dashboard where you can access the list of available proxies.
Next, select the Socks5 proxy option from the menu and choose a server location that best suits your needs. After selecting a server, you will be provided with detailed instructions on how to configure your device or browser settings to connect to the chosen proxy.
Follow these instructions carefully, inputting the required information such as IP address, port number, username, and password. Once set up correctly, your internet traffic will be routed through Wingate.me’s secure Socks5 proxy server seamlessly.
By utilizing Wingate.me’s Socks5 proxy, you can enjoy enhanced anonymity and protection while browsing online.
Conclusion
In a world where online privacy and security are paramount, having access to a reliable socks5 proxy list like Wingate.me is essential. By utilizing Wingate.me’s private proxy services, you can enhance your online anonymity and protect your sensitive information from prying eyes.
With various types of private proxies available, including socks5 proxies, Wingate.me offers flexibility and customization to suit your specific needs. Whether you’re looking to bypass geo-restrictions, improve your browsing speed, or simply add an extra layer of security to your online activities, Wingate.me has got you covered.
Setting up Wingate.me’s socks5 proxy is quick and easy, allowing you to start benefiting from enhanced privacy and security in no time. Simply follow the straightforward instructions provided by Wingate.me to configure the socks5 proxy on your preferred device or browser.
Don’t compromise on your online safety – explore Wingate.me’s socks5 proxy list today and take control of your digital footprint. Stay protected, stay secure with Wingate.me!
-
Articles4 months ago
How Many Times Can You Regrow Green Onions
-
Fashion9 months ago
Opals in the USA: A Gemstone Transforming the Crystal Healing Market
-
News11 months ago
Understanding HotLeaks: What You Need to Know
-
Entertainment8 months ago
How to Use Snaptik: A Complete Guide to Download TikTok Videos
-
Technology1 year ago
The Wonders of Oh Em Gee Blog
-
Entertainment1 year ago
Bare it All: Unforgettable Skinny Dipping Stories Shared
-
Health1 year ago
Can You Smoke Shrooms? Exploring the Myths and Realities
-
Busniess5 months ago
Why Is Business Part of Science: Strategy, Innovation Explained