Technology
Exploring The Basics of Hot Die Forging
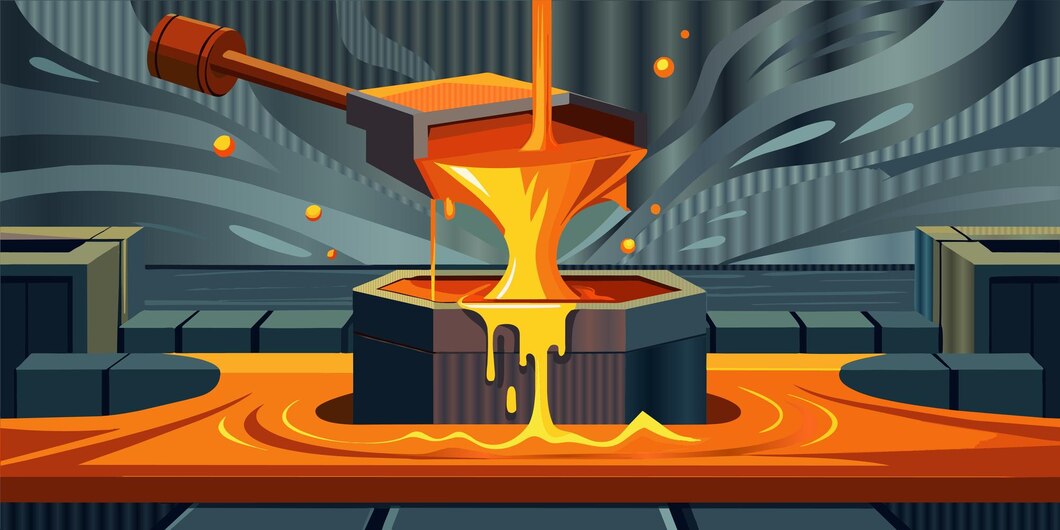
Introduction
Definition of Hot Die Forging
The Basics of Hot Die Forging is a manufacturing process that involves shaping metal using localized compressive forces at high temperatures. The process enhances the material’s mechanical properties, making it suitable for high-stress applications.
Importance of Hot Die Forging
The Basics of Hot Die Forging is crucial in producing high-strength components that are integral to various industries, including automotive, aerospace, and industrial machinery. Its ability to produce precise, durable parts makes it a preferred manufacturing method.
Overview of Article
This article will explore Hot Die Forging comprehensively, covering its definition, types, materials, process, advantages, applications, technical specifications, challenges, innovations, future prospects, comparative analysis, user guides, expert insights, and case studies.
What is The Basics of Hot Die Forging?
Definition and Explanation
Hot Die Forging is a metal forming process performed at high temperatures where the material is heated above its recrystallization point. This allows the metal to be deformed more easily, resulting in improved grain structure and mechanical properties.
History and Evolution
The origins of forging date back to ancient times, but Hot Die Forging, as a specialized process, has evolved significantly. Innovations in heating technology and material science have enhanced its efficiency and application scope.
Types of Forging
Hot Die Forging
Hot Die Forging involves heating the workpiece to a high temperature before applying compressive forces. This process is ideal for complex shapes and high-strength applications.
Cold Forging
Cold Forging is performed at or near room temperature. It offers advantages in terms of material properties but requires higher forces and is less suitable for complex shapes.
Warm Forging
Warm Forging is carried out at temperatures between cold and hot forging. It balances the advantages of both processes, offering good formability with less force and better mechanical properties.
Open Die Forging
In Open Die Forging, the workpiece is compressed between flat or simple-shaped dies. This method is used for large components and offers flexibility in shaping.
Closed Die Forging
Closed Die Forging involves compressing the workpiece within a die cavity that restricts metal flow, producing precise and complex shapes with high repeatability.
Materials Used in Hot Die Forging
Common Materials
- Steel (carbon, alloy, and stainless)
- Aluminum
- Titanium
- Nickel alloys
Material Properties
Materials used in Hot Die Forging must withstand high temperatures and deformation forces while retaining their mechanical properties. Key properties include high strength, toughness, and resistance to thermal fatigue.
Selection Criteria
Material selection depends on the desired properties of the final product, including strength, weight, corrosion resistance, and cost. Specific industry requirements also influence material choice.
The Hot Die Forging Process
Preparation
Preparation involves selecting and cutting the raw material to the required size and shape. Pre-forming operations may also be conducted to ease the forging process.
Heating
The workpiece is heated to a temperature above its recrystallization point, typically between 950°C and 1250°C, depending on the material. Controlled heating ensures uniform temperature distribution.
Forming
The heated workpiece is placed in the die and subjected to compressive forces from a hammer or press. The metal flows and fills the die cavity, forming the desired shape.
Cooling
After forming, the workpiece is cooled, often using controlled cooling techniques to enhance mechanical properties and prevent defects.
Finishing
Finishing operations, such as trimming, machining, and heat treatment, are performed to achieve the final dimensions and surface quality of the forged part.
Advantages of Hot Die Forging
Strength and Durability
Hot Die Forging produces components with superior strength and durability due to the refined grain structure and reduced porosity.
Material Efficiency
The process minimizes material waste and optimizes the use of raw materials, making it cost-effective for high-volume production.
Precision and Accuracy
Hot Die Forging can produce complex shapes with tight tolerances, ensuring high precision and consistency in the final products.
Applications of Hot Die Forging
Automotive Industry
Hot Die Forging is widely used to manufacture critical automotive components such as crankshafts, connecting rods, and gears, offering high strength and reliability.
Aerospace Industry
In the aerospace sector, Hot Die Forging produces parts like turbine blades, landing gear components, and structural elements, where high strength-to-weight ratio is essential.
Industrial Equipment
Components for industrial machinery, such as hydraulic presses, mining equipment, and construction machinery, benefit from the enhanced properties achieved through Hot Die Forging.
Consumer Goods
Hot Die Forging is also used in producing durable and high-quality consumer goods, including tools, hardware, and sporting equipment.
Technical Specifications
Temperature Requirements
Hot Die Forging requires precise temperature control, typically between 950°C and 1250°C, to ensure optimal material properties and prevent defects.
Pressure Requirements
The process involves applying high compressive forces, ranging from several tons to thousands of tons, depending on the material and component size.
Equipment Used
Key equipment includes forging presses, hammers, furnaces, and dies. Advanced machinery with precise control systems enhances process efficiency and product quality.
Challenges in Hot Die Forging
Temperature Control
Maintaining consistent and uniform temperatures is crucial to prevent defects such as cracks and incomplete filling.
Tool Wear
High temperatures and pressures cause significant wear on forging tools and dies, necessitating regular maintenance and replacement.
Material Defects
Defects such as cracks, voids, and inclusions can occur during forging, impacting the final product’s integrity and performance.
Latest Innovations in Hot Die Forging
Advanced Materials
Development of new alloys and materials with superior properties enhances the performance and application range of forged components.
Automation and Robotics
Automation and robotic systems improve process efficiency, precision, and repeatability while reducing labor costs and human error.
Simulation and Modeling
Advanced simulation and modeling tools enable precise process optimization, predicting material flow, temperature distribution, and potential defects.
Future Prospects of Hot Die Forging
Emerging Technologies
Emerging technologies such as additive manufacturing and hybrid forging methods promise to revolutionize the industry, offering new possibilities for complex and high-performance components.
Industry Trends
Trends towards lightweight materials, sustainability, and increased efficiency drive innovation in forging processes and materials.
Sustainability Considerations
Efforts to reduce energy consumption, material waste, and environmental impact are shaping the future of Hot Die Forging, with a focus on sustainable practices.
Comparative Analysis
Hot Die Forging vs. Cold Forging
The Hot Die Forging allows for more complex shapes and higher material strength, while Cold Forging offers better surface finish and dimensional accuracy but requires higher forces.
Hot Die Forging vs. Warm Forging
Warm Forging provides a balance between formability and material properties, with less force required than Cold Forging and better precision than Hot Die Forging.
Hot Die Forging vs. Casting
Hot Die Forging produces components with superior mechanical properties and less porosity compared to casting, making it suitable for high-stress applications.
User Guides
Step-by-Step Guide to Hot Die Forging
A detailed guide covering the preparation, heating, forming, cooling, and finishing stages of Hot Die Forging, including tips for achieving optimal results.
Maintenance Tips for Forging Equipment
Regular maintenance practices to ensure the longevity and performance of forging equipment, including inspection, lubrication, and tool replacement.
Safety Precautions in Hot Die Forging
Essential safety measures to prevent accidents and injuries, including proper protective gear, equipment handling, and emergency procedures.
Expert Insights
Quotes from Industry Experts
Insights and advice from leading experts in the forging industry on best practices, innovations, and future trends.
Best Practices and Recommendations
Recommendations for optimizing the Hot Die Forging process, including material selection, temperature control, and quality assurance.
Case Studies
Successful Implementation in Automotive Industry
A case study highlighting the successful use of Hot Die Forging in manufacturing high-performance automotive components.
Aerospace Industry Applications
Examples of Hot Die Forging applications in the aerospace sector, demonstrating the benefits of the process in producing lightweight and durable parts.
Innovations in Industrial Equipment Manufacturing
Case studies showcasing innovative uses of Hot Die Forging in producing advanced industrial machinery components.
Conclusion: The Basics of Hot Die Forging
Summary of Key Points
A recap of the essential aspects of Hot Die Forging, including its definition, process, advantages, applications, and future prospects.
Final Thoughts on Hot Die Forging
Reflections on the importance and potential of Hot Die Forging in various industries, emphasizing its role in advancing manufacturing technology.
Call to Action
Encouragement to explore further education and investment in Hot Die Forging technology, highlighting resources and opportunities for industry professionals.
Technology
SCMCompile: The Guide to Streamlining Your Supply Chain
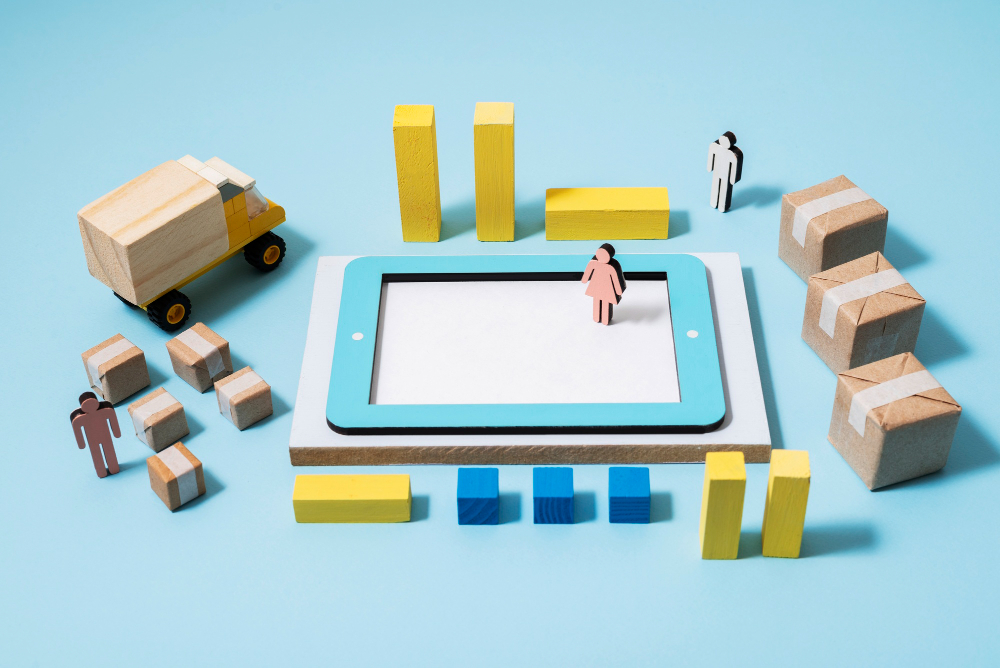
In today’s rapidly evolving business landscape, efficient supply chain management is no longer just an option; it’s a necessity. Companies that excel in optimizing their supply chain processes not only cut costs but also shorten delivery times, boost customer satisfaction, and ultimately gain a significant competitive advantage. One innovative tool making waves in this arena is SCMCompile.
But what exactly is SCMCompile, and how does it revolutionize supply chain operations? In this comprehensive guide, we’ll explore its standout features, notable benefits, real-world applications, and effective strategies for successful implementation.
What Is SCMCompile?
SCMCompile is a cutting-edge supply chain management optimization tool designed to streamline and enhance the workflows of supply chains through automation and intelligent analytics. Here’s what SCMCompile can do for your business:
-
Automate Procurement & Inventory Management: Say goodbye to manual tracking.
-
Optimize Logistics & Distribution: Find the fastest routes with minimal costs.
-
Slash Operational Costs: Leverage data-driven insights to improve efficiency.
-
Enhance Supplier Collaboration: Foster better communication with vendors.
What sets SCMCompile apart from traditional SCM software is its integration of AI and machine learning capabilities. These technologies empower businesses to predict demand fluctuations, identify inefficiencies, and make real-time adjustments.
Why SCMCompile Matters for Modern Supply Chains
Today’s supply chains are fraught with challenges, including:
-
Demand Volatility: Sudden shifts in market demand disrupt planning.
-
Supplier Delays: Geopolitical issues and logistics bottlenecks cause unforeseen delays.
-
Cost Pressures: Increasing fuel and labor costs squeeze profit margins.
SCMCompile addresses these challenges head-on through:
-
Predictive Analytics: Forecast demand accurately using historical data and trends.
-
Automated Replenishment: Automatically triggers orders when inventory dips below a defined threshold.
-
Route Optimization: Finds the most efficient shipping routes for cost savings.
Real-World Impact: Retail Giant Reduces Costs by 15%
For instance, a leading retail chain adopted SCMCompile and achieved impressive results:
-
15% reduction in excess inventory
-
20% faster order fulfillment
-
10% lower logistics costs
These results showcase how innovative tools like SCMCompile can lead to significant ROI.
Key Features of SCMCompile
-
AI-Driven Demand Forecasting:
-
Leverages past sales, seasonality, and market indicators for accurate demand predictions.
-
Automatically adjusts inventory levels to prevent stockouts and overstock situations.
-
-
Smart Procurement Automation:
-
Automates negotiations with suppliers to secure bulk discounts.
-
Flags potential disruptions, like adverse weather, to manage expectations.
-
-
Real-Time Logistics Optimization:
-
Integrates with GPS and traffic data to suggest immediate route adjustments.
-
Recommends alternative carriers if disruptions occur.
-
-
Supplier Performance Tracking:
-
Monitors vendor performance based on delivery speed, product quality, and pricing.
-
Suggests alternative suppliers if a vendor’s performance dips below standards.
-
-
Blockchain for Supply Chain Transparency:
-
Ensures traceability in compliance-heavy industries such as pharmaceuticals and food.
-
How to Successfully Implement SCMCompile
Step 1: Assess Your Current Supply Chain
-
Identify and analyze bottlenecks (e.g., slow supplier response times).
-
Define Key Performance Indicators (KPIs) such as order cycle time and fill rate.
Step 2: Integrate with Existing Systems
-
Ensure compatibility with your current ERP (like SAP or Oracle), Warehouse Management Systems (WMS), and Transportation Management Systems (TMS).
Step 3: Train Your Team
-
Conduct workshops to help staff interpret AI-driven recommendations.
-
Create incentives to encourage team members to adopt the new system.
Step 4: Monitor & Optimize
-
Regularly track key performance metrics and refine algorithms as more data becomes available.
Addressing Potential Challenges
While implementing new technology, businesses may face challenges such as:
-
Resistance to Change: Engage your teams early to promote buy-in.
-
Data Quality Issues: Cleanse outdated data before migrating to the new system.
-
High Initial Costs: Initiate a pilot program to demonstrate potential ROI before full implementation.
The Future of SCMCompile and Supply Chain Technology
Experts predict that the future will see further integration of technologies like AI, IoT, and blockchain reshaping SCM. Upcoming trends include:
-
Autonomous Logistics: Think self-driving trucks and drone deliveries.
-
Hyper-Personalized Supply Chains: Custom packaging and swift last-mile delivery solutions.
-
Sustainability Analytics: Monitoring carbon footprints and promoting eco-friendly practices.
Final Thoughts: Is SCMCompile Right for Your Business?
If your organization struggles with issues such as:
-
Excess inventory costs
-
Late shipments
-
Supplier reliability challenges
Then SCMCompile could be a transformative solution for your supply chain management. Start with a trial, assess the improvements, and gradually scale the implementation.
Pro Tip: Pair SCMCompile with a robust change management strategy to maximize adoption and achieve standout results.
Technology
A Guide to Planning a Multilingual Online Event
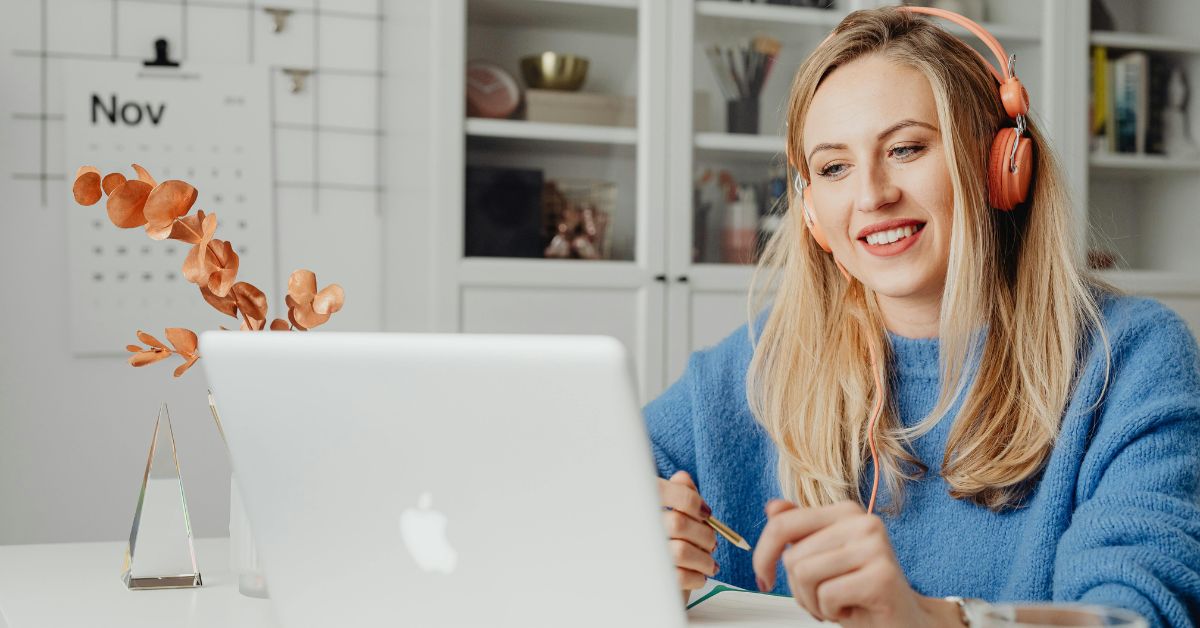
When people connect from different parts of the world, it’s only natural that they don’t all speak the same language. Still, it’s increasingly common for them to share the same screen. The rise of global meetings, digital conferences, product launches, and hybrid events is removing physical barriers—but it’s also challenging us to rethink how we communicate. A stable internet connection and a user-friendly platform are no longer enough. Effective communication in remote events now requires considering what each participant hears, sees, and understands—regardless of the language they think in.
Why Language Decisions Should Be Made Early
One of the most common mistakes in planning virtual events is leaving the language component until the end. In reality, language should be considered from the very first draft of the event. This doesn’t just mean deciding whether to include subtitles, live interpretation, or voiceover—it means understanding the expectations of your audience, their roles, and how they’ll interact.
One thing truly global events have in common is that they view their audience as a diverse group with varying levels of language fluency—and they actively work to include everyone in the experience. This is achieved by combining a variety of tools and services that make up the current landscape of language solutions. There’s no one-size-fits-all approach. It’s about identifying the best format for each type of content, determining what’s technically feasible, and ensuring a consistent, high-quality experience for all participants.
When to Use Subtitles, Interpretation, or Voiceover
Not every strategy works for every event. The key is selecting the right tool for the type of communication you’re delivering. For events with single speakers and linear presentations, simultaneous interpretation is often the best choice. It allows each attendee to choose their preferred audio channel and listen in real time in their own language. However, this setup requires reliable technical infrastructure, professional interpreters, and pre-event coordination with speakers.
For more visual events—or ones where accuracy is critical, such as technical product launches or training sessions—real-time subtitles might be a better fit. They support viewers who partially understand the original language and enhance accessibility for people with hearing impairments. In these cases, fast, clear, and accurate transcription is essential.
Voiceover, though less common for live events, can be valuable for pre-recorded webinars or content that will be shared post-event. Its main advantage is delivering a fully localized experience, though it requires more time and editing. Some companies even combine formats—offering live interpretation during the event and a dubbed version for on-demand distribution later.
The Limits of Machine Translation for Live Events
AI-powered tools have greatly expanded the availability of automatic translation and subtitling. While they can be helpful in informal settings, they still have major limitations when it comes to quality, nuance, and context. In most professional or corporate settings, automated translation should be used with caution.
Human input is still crucial for ensuring accuracy and adapting tone, cultural references, and expressions. A trained interpreter can convey intent and emotion in ways that algorithms simply can’t—at least not yet. So while technology can assist, suggest, or accelerate certain tasks, it does not replace the need for thoughtful planning and expert curation in serious multilingual events.
Technical implementation also requires attention. Choosing a streaming or video conferencing platform that supports multiple audio tracks, interpretation channels, or synchronized subtitles is not a trivial decision. Specialized tools exist for this, and testing them well in advance is highly recommended.
Preparing the Tech Team and Interpreters
Beyond technology, events are still a human experience. That means the team involved needs to be properly prepared. If your event includes live interpreters, it’s essential to provide them with all presentation materials in advance, clearly define their shifts, and ensure they have an appropriate acoustic and technical setup. The same goes for moderators and presenters: they must know how to activate multilingual features, guide the audience, and answer common participant questions.
In large events or ones with multiple simultaneous sessions, it can be helpful to assign a dedicated language coordination manager. This person ensures that each language channel is running smoothly and can assist attendees facing technical issues. Their role becomes even more valuable when the audience includes participants with limited digital literacy or accessibility challenges.
Multilingual Virtual Event Planning Checklist
Planning a multilingual online event can be complex—but much easier when you follow a clear roadmap. This checklist offers a foundational guide to help you deliver a smooth, professional experience:
Before the event:
- Define the primary languages and delivery methods (audio, subtitles, voiceover)
- Choose experienced providers for interpretation, subtitling, or dubbing
- Confirm that your platform supports multiple audio tracks and/or subtitles
- Train the technical team and moderators on multilingual features
- Run a full event rehearsal including interpretation or subtitling
- Send interpreters all relevant materials: presentations, glossaries, agenda
During the event:
- Activate and test language channels before going live
- Guide attendees on how to access their preferred language
- Set up a tech support channel to handle attendee questions
- Monitor audio quality across all channels
- Coordinate interpreter transitions for long sessions
After the event:
- Evaluate the quality of interpretation or subtitles
- Collect feedback from attendees on their language experience
- Use feedback to improve future events
- Prepare edited versions with dubbing or subtitles for post-event sharing
- Publicly thank your language and technical teams
Beyond Language, It’s About What You Share
Thinking in multiple languages isn’t just a nice-to-have—it’s a way to design more inclusive events where ideas aren’t lost in translation but flow freely. The strength of a global audience lies in its diversity, and each language is a doorway into that shared conversation. Planning with this in mind can be the difference between a meeting that’s simply heard—and one that’s truly understood.
Technology
The Scale Blank: How to choose Perfect One for Your Needs
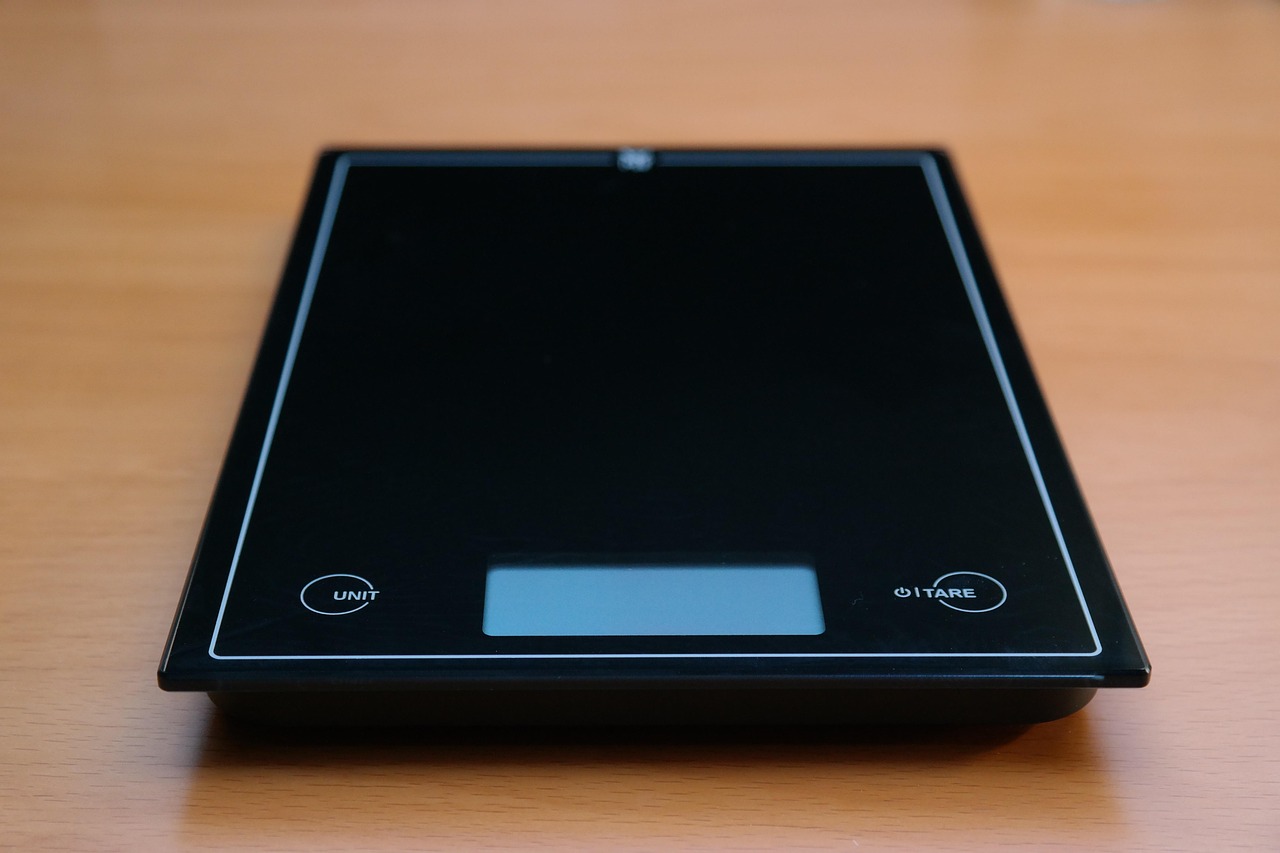
Have you ever wondered why some kitchen scales perform flawlessly while others fail within months? The secret often lies in an overlooked component—the scale blank. Whether you’re a home cook, a professional chef, or a business owner, choosing the right scale blank can make all the difference in accuracy, durability, and performance.
In this guide, we’ll break down everything you need to know about scale blanks—what they are, why they matter, and how to pick the best one for your needs.
What Is a Scale Blank?
A scale blank is the foundational platform of a weighing scale where items are placed for measurement. It’s the flat surface (usually made of stainless steel, glass, or plastic) that interacts directly with whatever you’re weighing.
Why Does It Matter?
-
Accuracy: A poorly designed blank can flex or warp, leading to incorrect readings.
-
Durability: The material determines how well it resists scratches, stains, and wear.
-
Hygiene: Some blanks are easier to clean, making them ideal for food or medical use.
Types of Scale Blanks: Pros and Cons
Not all scale blanks are created equal. Here’s a breakdown of the most common types:
1. Stainless Steel Blanks
✅ Pros:
-
Highly durable and resistant to corrosion
-
Easy to clean (ideal for kitchens and labs)
-
Provides a stable weighing surface
❌ Cons:
-
Can be slippery for lightweight items
-
Prone to fingerprints and smudges
Best for: Commercial kitchens, laboratories, and industrial settings.
2. Glass Blanks
✅ Pros:
-
Sleek, modern appearance
-
Easy to wipe clean
-
Doesn’t absorb odors or stains
❌ Cons:
-
Fragile—can crack under heavy weight
-
Slippery for certain items
Best for: Home kitchens, bakeries, and retail displays.
3. Plastic Blanks
✅ Pros:
-
Lightweight and affordable
-
Resistant to minor impacts
-
Non-slip surface in some models
❌ Cons:
-
Less durable over time
-
Can absorb stains and odors
Best for: Budget-friendly home scales or portable options.
How to Choose the Right Scale Blank
Picking the best scale blank depends on your specific needs. Here’s what to consider:
1. Intended Use
-
Cooking/Baking? Stainless steel or glass for easy cleaning.
-
Industrial Weighing? Reinforced stainless steel for durability.
-
Portable Scale? Lightweight plastic for convenience.
2. Weight Capacity
-
Small kitchen scales (1–10 lbs): Glass or plastic.
-
Heavy-duty scales (50+ lbs): Thick stainless steel.
3. Maintenance & Cleaning
-
Stainless steel: Wipe with a damp cloth.
-
Glass: Use glass cleaner for shine.
-
Plastic: Avoid abrasive cleaners to prevent scratches.
4. Anti-Slip Features
Some blanks have textured surfaces or rubberized edges to prevent items from sliding off.
5. Budget
-
Premium: Stainless steel
-
Mid-range: Tempered glass
-
Budget-friendly: High-quality plastic
Real-World Examples: Where Scale Blanks Make a Difference
Example 1: Bakery Business
A bakery switched from plastic to stainless steel blanks and saw fewer inaccuracies in dough measurements, leading to more consistent products.
Example 2: Home Cooks
A home chef using a glass scale blank found it easier to clean after measuring sticky ingredients like honey or syrup.
Example 3: Lab Environments
A research lab using high-grade stainless steel blanks avoided corrosion from chemical spills, ensuring long-term reliability.
Expert Tips for Maintaining Your Scale Blank
To extend the lifespan of your scale blank:
✔ Clean regularly—avoid buildup of debris.
✔ Avoid overloading—stick to the maximum weight limit.
✔ Store properly—keep in a dry place to prevent rust (for metal blanks).
✔ Check for damage—cracks or warping can affect accuracy.
Final Thoughts: Why Your Scale Blank Choice Matters
The scale blank might seem like a small detail, but it plays a crucial role in the accuracy and longevity of your weighing scale. Whether you’re a home cook, a business owner, or a lab technician, choosing the right material and maintaining it properly ensures reliable measurements every time.
Ready to upgrade your scale? Now that you know what to look for, you can make an informed decision and get the best performance out of your weighing device.
FAQs About Scale Blanks
Can I replace a damaged scale blank?
Yes, many manufacturers sell replacement blanks. Check compatibility before purchasing.
Are there antimicrobial scale blanks?
Some stainless steel blanks have antimicrobial coatings, ideal for medical or food industries.
How do I know if my scale blank is affecting accuracy?
If your scale gives inconsistent readings, inspect the blank for warping or damage.
-
Articles5 months ago
How Many Times Can You Regrow Green Onions
-
Fashion10 months ago
Opals in the USA: A Gemstone Transforming the Crystal Healing Market
-
News1 year ago
Understanding HotLeaks: What You Need to Know
-
Entertainment9 months ago
How to Use Snaptik: A Complete Guide to Download TikTok Videos
-
Technology1 year ago
The Wonders of Oh Em Gee Blog
-
Entertainment1 year ago
Bare it All: Unforgettable Skinny Dipping Stories Shared
-
Health1 year ago
Can You Smoke Shrooms? Exploring the Myths and Realities
-
Busniess5 months ago
Why Is Business Part of Science: Strategy, Innovation Explained